If you do
NOT see the Table of Contents frame to the left of this page, then
Click here to open 'USArmyGermany'
frameset |
US
Army Medical Materiel Center, Europe
7th Medical Command
Looking for more information from military/civilian
personnel assigned to or associated with the U.S. Army
in Germany from 1945 to 1989. If you have any
stories or thoughts on the subject, please contact me .
|
|
|
|
|
USAMMCE
History |
|
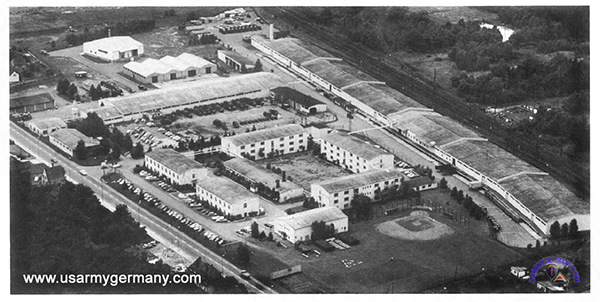
US Army Medical Materiel Center, Europe, before 1970
|
|
(Source: Official USAMMCE website) |
The US Army Medical Materiel Center, Europe (USAMMCE) was activated as the Rhein Medical Depot in December 1951 at Einsiedlerhof, Germany.
In the Spring of 1957, the Rhein Medical Depot was reorganized as the United States Army Medical Depot, Einsiedlerhof (USAMDE) and assumed operational control of the 67th Medical Depot.
USAMDE
and the Medical Supply Division of the United States Army, Europe were combined to form the United States Medical Materiel Center, Europe in October 1968.
USAMMCE moved to its current location in Pirmasens in November 1975 as part of an Army-Air Force re-stationing initiative.
The following medical supply, optical, and maintenance (MEDSOM) battalions were formed as subordinate units to USAMMCE in January 1980:
37th MEDSOM to support the US V Corps
428th MEDSOM to support the US VII Corps
226th MEDSOM to support the Communications Zone
USAMMCE was designated as the Theater Single Integrated Medical Logistics Manager in June 1986 and assumed the medical logistics support responsibility for all US Armed Forces serving in the US European Command.
The 226th MEDSOM was re-designated as the 226th Medical Logistics Battalion (Logistics, Rear); the 37th MEDSOM was re-designated as the 37th Medical Detachment (Logistics); and the 428th MEDSOM was re-designated as the 428th Theater Medical Materiel Management Center (TMMMC) in June 1993.
In October 1994, the 226th Medical Battalion (Logistics, Rear) was re-designated as the 226th Medical Battalion (Logistics, Forward) and was assigned to the 30th Medical Brigade; the 37th Medical Detachment and the 428th TMMMC were inactivated.
Upon the inactivation of the US Army’s 7th Medical Command, USAMMCE was assigned to the US Army Medical Research and Materiel Command in October 1994.
USAMMCE became the Executive Agent for the Department of State’s Humanitarian Assistance Program on 1 October 1996.
USAMMCE received the Vice Presidential Hammer Award on 17 June 1997 for setting new standards of excellence in supporting its customers and supporting the concepts of President Clinton’s Reinvention of Government initiative.
USAMMCE PAST AND PRESENT
DECEMBER 1951 – Rhein Medical Depot activated at Einsiedlerhof, Germany
MARCH 1953 – 67th Medical Depot assigned operational control of the Rhein Medical Depot
OCTOBER 1956 – Rhein Medical Depot reassigned to USAREURCOMMZ. 67th Medical Depot and 8040th Civilian Labor Group (CLG) also assigned to USAREURCOMMZ.
APRIL 1957 – Rhein Medical Depot inactivated. US Army Medical Depot, Einsiedlerhof (USAMDE) organized and assigned to USAREUR.
MAY 1957 – 67th Medical Depot attached to USAMDE for Administration Operations, and Logistical Support.
JANUARY 1959 – USAMDE designated a subordinate command of ADSEC, USAREURCOMMZ. ADSEC re-designated as Theater Army Support Command, Europe on 28 February 1960 and TASCOM, 4th Logistical Command.
DECEMBER 1963 – 4TH Logistical Command inactivated and USAMDE designated a subordinate command of USACOMMZEUR.
OCTOBER 1968 – The Medical Supply Division of USACOMMZEUR and the US Army Medical Depot, Einsiedlerhof were combined to form the US Army Medical Materiel Center, Europe (PROV).
NOVEMBER 1975 – The unit completed relocation to Husterhoeh Kaserne, Pirmasens, Germany.
JULY 1985 – USAMMCE realigned to reflect three deputy commanders under one commander and added three Medical Supply, Optical, and Maintenance (MEDSOM) Battalions.
JUNE 1986 – USAMMCE assumed Tri-Service Class VIII mission for the United States European Command.
JUNE 1993 – USAMMCE’s force structure changed to reflect organization of the 428th Theater Medical Materiel Management Center and the 226th Medical Battalion (Logictics, Rear), and deactivation of the three MEDSOM battalions.
OCTOBER 1994 – Upon inactivation of the 7th Medical Command, USAMMCE came under the command and control of the United States Army Medical Research and Materiel Command, a major subordinate command of the United States Army Medical Command. The 226th Medical Battalion (Logistics Forward) came under the Command and Control of the 30th Medical Brigade, V (US) Corps.
JULY 1999 – The 226th Medical Battalion was relocated to Miesau, and USAMMCE remained as a Remote Site at Husterhoeh Kaserne.
The US Army Medical Materiel Center, Europe is located at Husterhoeh Kaserne, just at the Northern Edge of the city of Pirmasens, a few miles from the French border. Pirmasens is located in Rhineland-Palatinate (Rheinland-Pfalz). A state of the Federal Republic of Germany, commonly referred to as the Pfalz.
Date |
Action |
Authority |
1 Dec 51 |
Rhine Medical Depot activated at Einsiedlerhof Germay. |
EUCOM GO 29, 12 Oct 51 |
1 Jan 53 |
Electrical accounting machine procedures established for stock control accounting. |
|
2 Mar 53 |
67th Medical Depot assigned operational control of Rhine Medical Depot. |
USAREUR GO 12, 2 Mar 53 |
Dec 54 |
Warehouse facilities at railhead, Hoehmuehlbach occupied by Rhine Medical Depot. |
|
1 Oct 56 |
Rhine Medical Depot re-assigned to USARUER COMZ. |
USAREUR COMZ GO 72, 1 Oct 56 |
|
67Th Medical Depot and 8040th CLG also assigned to USAREUR COMZ. |
USAREUR Trp Asg memo 15 |
1 Apr 57 |
Rhine Medical Depot deactivated. US Army Medical Depot, Einsiedlerhof organized and assigned to USAREUR COMZ |
USAREUR GO 53, 1 Apr 57 |
6 May 57 |
67th Medical Depot attached to USAMDE for Administrative, operational, and logistical support. |
7th Army Trp Asg, Memo 3, para 13, 6 May 57 |
1 Jan 59 |
USAMDE designated a subordinate command of ADSEC, USAREUR COMZ. ADSEC re-designated as Theater Army Support Command Europe on 28 Feb 60. |
USAREUR COMZ ADSEC GO1, 1 Jan59 |
1 Jul 61 |
TASCOM re-designated 4th Logistical Command. |
|
1 Dec 63 |
4th Logistical Command inactivated and USAMDE Designated a subordinate Command of USACOMZEUR. |
USACOMZEUR Msg |
1 Apr 67 |
67th Medical Depot assigned to US Army Medical Depot, Einsiedlerhof. |
USACOMZEUR GO 101, 1 Jun 67 |
1 Jul 68 |
USAREUR Medical Command established Medical Command |
|
1 Oct 68 |
USAMDE deactivated. US Army Medical Materiel Center, Europe organized and assigned to US Army Medical Command, Europe. |
USAREUR GO 534, 26 Sep 68 |
1 Dec 69 |
234th Medical Detachment (GO) assigned to US Army Medical Materiel Center, Europe. |
USAMEDCOMEUR GO 51, 24 Nov 69 |
22 Sep 75 |
7th Combat Support Hospital assigned to USAMMCE. |
USAMEDCOMEUR GO 80, 17 Sep 75 |
1 Oct 75 |
US Army Medical Materiel Center, Europe relocated to Husterhoeh Kaserne, Pirmasens,GE. |
USAMMCE GO 7, 5 Aug 75 |
12 Nov 75 |
31st Combat Support Hospital assigned to USAMMCE. |
USAMEDCOMEUR GO 92, 12 Nov 75 |
|
|
|
1969 |
(Source: STARS & STRIPES, Sept 30, 1969) |
On Oct 1 1969, the US Army Medical Materiel Center, Europe will celebrate its first anniversary. USAMMCE was formed on Oct 1 1968 through the merger of the Medical Supply Division of the Supply & Maintenance Agency with US Army Medical Depot, Einsiedlerhof.
USAMMCE is located at Einsiedlerhof. The center is directly subordinate to the US Army Medical Command, Europe, which is located at Heidelberg. CO of USAMMCE is Col Frank D. Godwin.
USAMMCE has the mission of supplying and servicing all of the medical supplies and equipment in Europe.
The center is currently organized as follows:
Supply & Transportation Directorate
Maintenance Directorate
Optical Activities Directorate
Inventory Control Directorate
Comptroller Directorate
Administration & Service Directorate
Data Processing Directorate
S&T Directorate (headed by Lt Col Lester R. Boyd): stores 7,000 different items; ships more then 100,000 items annually to hospitals throughouit Europe; also responsible for storing (in vaults) precious metals (gold and silver) used by dentists as well as drugs for more serious medical cases.
Maint Directorate: restores medical equipment to serviceable condition; about 7,000 items repaired in the last year; provides direct maintenance support to 15 Medical Service Areas, comprising approx. 110 medical units throughout Europe. Also operates one of only three audiometer calibration centers in the US Army (hearing test equipment).
Inv. Control Directorate: responsible for the supply management function.
Comptroller Directorate: responsible for the financial management function.
The Inv. Control and Comptroller directorates jointly operate the Medical-Dental Stock Fund Sub-Home Office.
|
|
|
1970 |
(Source: USAREUR Medical Bulletin, March 1970) |
The US Army Medical Materiel Center, Europe, (USAMMCEUR) dates its history from June 1951. Established as the Rhine Medical Depot, the Center began operations under Headquarters, European Command as the only medical depot in Europe. Since activation, the depot has continued to operate at its location in Einsiedlerhof with only minor changes in name and mission.
In October 1968 the Center received its present name and was placed within the US Army Medical Command, Europe. With an authorized strength of nearly 500 persons, USAMMCEUR's mission is to provide all medical supplies and equipment used by the US Army in Europe, North Africa and the Middle East. This mission includes stock and inventory control, receipt, storage, and issue of medical supplies, fabrication of spectacles, and provision for medical maintenance support.
Functions involved in the execution of this mission include the accountability of all theater stock, stock control of operating and reserve stocks, and inventory management of the medical commodity. Basic supply and transportation functions include the receipt, storage and issue of medical supplies, the disassembly and reconstitution of medical assemblages, and the care and preservation of certain medical items.
The center also has responsibility for providing general support maintenance for command stocks, direct support maintenance for user organizations and overhaul of unserviceable equipment.
Another basic function of the Center is the fabrication of both standard and non-standard spectacles. USAMMCEUR supplies spectacles for the US Army, Europe, the US Air Force, Europe, and dependents within the European Command.
In order to assure that medical supplies and equipment are in satisfactory condition, the Quality Assurance Directorate performs the necessary quality inspections in optical, maintenance and supply; processes customer complaints affecting quality; and surveys mission and assembly stocks.
The US Army Medical Materiel Center, Europe, is commanded by Colonel Frank D. Godwin, MSC. COL Godwin assumed command of the Center in July 1966, having completed an assignment at Martin Army Hospital, Ft. Benning, Georgia, as Chief of the Supply and Services Division. |
|
If you have more
information on the history or organization of USAMMCE, please contact me . |
 |
|
|
Command
newspaper articles |
|
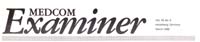 |
Medical Materials:
The Army's best-kept secret,
By
Irene Weber, March 1988 |
Located
on a hilltop in Pirmasens, the U.S Army Medical
Materiel Center, Europe (USAMMCE), is one of the
Army's best-kept secrets. A secret in the sense that most, who
use the medical supplies and equipment that originate from USAMMCE,
never realize the enormous effort involved in their procurement,
processing and distribution.
USAMMCE's overall peacetime misson is trifold: to furnish the
medical supply support; to provide maintenance support for medical
equipment; and optical fabrication to the Army, Navy, Air Force
and State Department activities found in Europe, Africa and
the Middle East. USAMMCE also supports military and diplomatic
personnel stationed within the Soviet Block.
Additionally, USAMMCE has a readiness mission that includes:
the replacement an maintenance of medical supplies and equipment
contained in the medical assemblages that would be issued to
U.S. units in the event of war in Europe; the stockage of war
reserves of medical supplies to resupply units in combat and
the planning for medical supply during the transition-to-war
period.
According to Col. Thomas E. Kistler, USAMMCE Commander, "the
scope of the mission is easier to understand if you look at
it in terms of sales. Last year, we issued $53 million worth
of materiel and maintained $113 million worth of inventory.
Also, we manufactured 162,000 pairs of glasses."
USAMMCE processes an average of 27,000 requests for medical
items each month and maintains an inventory of over 16,000 different
items. Most customer requests are routinely processed within
14 days. Special requests, such as those used to treat patients
in life or death situation, are processed more quickly.
"Most 'Life or Death' requisitions can be filled from supplies
already stocked at USAMMCE or shipped from the United States
within a 24 hour period," Kistler stated.
"The 'Life or Death' requisitions not available in-country can
be shipped from New York or Baltimore by commercial carrier
and hand-carried for pick up at Rhein Main Airport, Frankfurt,"
Kistler continued. "High priority requisitions (other than 'Life
or Death') are normally filled within 7 days. Normal requisitioning,
counting from the time of order to time of receipt, takes about
21 days." |
|
The
majority of medical supplies arrive at USAMMCE by Air Force
cargo pallets. These pallets are provided by depots maintained
in the continental U.S. and flown out of Dover Air Force Base,
Delaware. The supplies are flown to Ramstein AFB via Air Lines
of Communications (ALOC) and trucked to Pirmasens. USAMMCE receives
an average of 170 pallets per month.
Additionally, USAMMCE receives 40-50 vanloads of supplies on
a monthly basis. Medical supplies are also received by mail.
The physical scope of USAMMCE is quite staggering. Sprawled
across 93 acres of hilltop, is a wide assortment of buildings,
warehouses, equipment depots and storage sheds. The warehouses
contain over 800,000 square feet of storage space and are divided
into heated, unheated and refrigerated storage areas.
One of the most interesting warehouses is the one that houses
USAMMCE's stored medical supplies. Here, in what is called the
"bin storage", can be found an assortment of medical and dental
supplies ranging from gauze to alcohol swabs. Pilferable items,
such as injection needles or other small, sensitive items, are
kept in a fenced-in area of the bin known as the "cage". All
security items, such as dental gold or any controlled medical
supply, are housed in what is called the "vault". The areas
containing drugs are maintained at a constant temperature to
ensure the effectiveness of the medications.
Also, located in this warehouse is the storekeeping section.
Stored here are 15,000-16,000 different item locations. Many
of these items are kept in multi-story rotary bins operated
by the push of a button.
These new rotary bins have cut down both time and work load
for the 30 employed in this warehouse. These bins can contain
12,000 additional locations. Workers here process an average
of 1200 customer orders each day. These customer orders are
called Medical Release Orders (MROs). MROs represent issues
that are processed for the 430 customer units supported by USAMMCE.
|
|
|
Distribution
and transportation
In June 1986, the Army implemented Tri-Service support. Since
that time, there has been a steadily increasing demand for supplies.
Once an MRO has been selected and packed, it is released to
the Transporation Division for shipment to the customer. This
division is part of the Directorate of Distribution and Transportation.
Transportation is responsible for the planning, coordination
and supervision of all shipments from USAMMCE.
Transportation not only checks, consolidates and repacks supplies
prior to their shipment, but it is also responsible for the
selection of the mode of transportation to be used.
The types of transportation used vary and are as follows: 80%
of all medical supplies from USAMMCE are transported by truck,
15% are flown by either military or civilian aircraft, 3% are
sent by Parcel Post, 1% is sent UPS and 1% is sent by rail.
The type of transportation depends on the supply's destination.
To help make loading and shipping easier and more time efficient,
Kistler, in 1979, suggested a method called "Shrink Wrap". Shrink
Wrap looks like ordinary, kitchen plastic wrap, but it is used
at USAMMCE to wrap around stacks of medical supplies. Not only
does the Shrink Wrap make loading and shipping easier by allowing
the supplies to be bound together, stacked higher and protected,
but it is also transparent. This transparency enables the supplies
to be easily viewed and stocking mistakes are less likely to
be made.
Assembly and reconstitution
One of the most amazing sections at USAMMCE is the Assembly
and Reconstitution Division, part of USAMMCE's Directorate of
Operations. The Assembly and Reconstitution Division is responsible
for reconstituting all medical assemblages ranging in size from
first aid kits to complete field hospitals.
Last year, they built two 500-bed hospitals and they routinely
build 200-bed hospitals. It takes two teams, or a total of 28
people, approximately 4 months to build a 500-bed hospital.
According to Cpt. Irene Logan, chief of Assembly and Reconstitution,
"Our biggest problem is getting the requisitions from the U.S.
quickly. We're hard workers here, we get the job done."
The reconstitution of old sets requires checking for items no
longer needed or obsolete and the inspection of all items. This
inspection is to guarantee the continued usefulness and effectiveness
of an item. If the item fails inspection it must be replaced.
"We check the life-cycle of supplies," Logan explained. "Even
band-aids are inspected. As long as they stick, they're good."
The Readiness Division of USAMMCE also falls under the Directorate
of Operations. This division is reponsible for the management
of medical assemblages owned and stored by the Combat Equipment
Group, Europe (CEGE) as POMCUS and for decrement assemblages
owned and stored by USAMMCE.
The Pre-Positioning Of Material Configured to Unit Sets (POMCUS)
consists of material stored at various sites that is ready for
units from the U.S. to fall in on it. Decrement assemblages
consist of medical equipment necessary for 7th MEDCOM hospitals
to displace from their peacetime facilities and operate in the
field.
The Readiness division also provides technical surveillance
of the medical equipment and materials in warm-base hospitals
and is the caretaker for 7th MEDCOM contingency hospitals. A
warmbase hospital is a POMCUS hospital maintained by CEGE. It
is a physical structure with equipment already available; all
that is needed is for personnel to move in. A warm-base hospital
saves time and money because it is already erected. Any structure
can be adapted. All that is needed is sufficient space, electrical
lines and a water source.
A contingency hospital is a decrement hospital maintained by
USAMMCE. Equipment and stock are stored and maintained in the
event of a possible but uncertain need. USAMMCE is the caretaker
for the 7th MEDCOM contingency hospitals.USAMMCE is also responsible
for the fabrication of spectacles and optical inserts for all
DOD personnel and their dependents. In addition, the optical
laboratory provides civilian-type frames for eligible personnel.
|
|
Quality
control
Quality is a major concern in the optical department as well
as throughout USAMMCE. Optical standards are closely monitored
by the Directorate of Quality Control (QC) at USAMMCE. QC performs
a 100 percent inspection of all optical appliances manufactured.
All optical fabrications must meet the F.D.A. standard, Z-80,
or it is not sent out to the consumer. In fact, the quality
of work is so high, they have only a 0.94 return rate. This
represents less than one pair per 1,000 spectacles returned.
"All of us here at QC, we're called the bad guys", chuckled
Sgt. Samuel King, NCOIC of Optical Quality Control. "We keep
a running list of goods. If the glasses don't meet the standard,
they don't go out. We want to be known for our high quality."
The Directorate of Quality Control is headed by Herr Harry Schindler,
a member of the 8040th Civ. Support Group, who reports directly
to the commander. The Directorate of QC at USAMMCE is the largest
of its kind in the U.S. Army Medical Department.
QC is responsible for the inspection of the medical supplies
received, stored and issued, as well as, all equipment reconditioned
by the Medical Maintenance Shops. The QC division checks everything
that is accomplished at USAMMCE; no department escapes their
close scrutiny.
Acknowledged Schindler, "We leave nothing to chance, we inspect
prior to issue so that there will be greater customer satisfaction."
The QC division has three main missions. In addition to inspection
of all topics, they are responsible for supply and maintenace
control.
The supply side of QC inspects a representative sampling of
outgoing shipments in an effort to guarantee that the highest
possible standard is met. They inspect material received from
CONUS depots and vendors to ensure that the correct items and
quantities are received and that they are properly packed, marked
and serviceable.
QC is also reponsible for cyclical surveillance of supply items.
A close watch is kept on expiration dates of medications and
shelf-life of materials stocked at USAMMCE.
The Maintenance Division of QC performs a 100 percent final
inspection on items before they are issued to the customer.
They inspect repaired and stored medical equipment prior to
issue, change condition classifications on items and equipment
and reconstitute such items as batteries for x-ray machines
and equipment odometers.
The QC Support Division acts as the main focal point in Europe
for medical material complaints. This division not only receives
input from CONUS, but also issues quality control directives
throughout Europe.
These directives may contain any of the following: an extension
authority for potency dated items, suspension instructions,
drug recalls, warning notices for hazardous conditions and destruction
notices for suspect material. They are also responsible for
customer complaints as well as ensuring customer satisfaction.
"The in-house control is tight," says Schindler. "The patient
and health care providers need the best material. We are here
to see that they get it when they need it. Our concern is customer
satisfaction."
Modernizations at USAMMCE also help to create greater chance
for customer satisfaction, but recent budget cuts have hit even
this facility. The result is that their mission, difficult as
it is, is now even more difficult.
At the beginning of FY 88, USAMMCE's recognized manpower requirements
totaled 702 (employees). Of the 702 recognized, only 638 positions
were authorized. Currently, USAMMCE has 641 personnel assigned
including overhires. USAMMCE is able to fulfill its mission
of supplying medical support, optical support and medical maintenance
support to all of its customers even with a shortage of 61 recognized
positions.
When asked what represents the biggest obstacle for a commander
to overcome at USAMMCE, Kistler responded simply,"A lack of
people."
Summing up USAMMCE's role, Maj. Larry Browning, Deputy for Administration,
replied, "USAMMCE is one of a kind. There's not another like
it. We provide all the medical supply support to Europe, the
Far East and Africa. Added to this, we do optical fabrication.
Once you can accept this mission and realize that we do this
with a total of only 641 employees (390 civilian, 251 military),
then you can understand USAMMCE. We perform our mission well
and we perform it as a family." |
|
 |
|
|
COMMENTS
on USAMMCE |
|
Additional
information provided by George O'Brien who served in the ADP Division,
USAMMCE.
I was assigned to Einsiedlerhof from 1969-1973 in the ADP Machine
Br. We provided ADP support for the depot. As I recall we shipped
medical supplies to an area that stretched from Iceland to Moscow,
on an east-west axis, and from Sweden to Morrocco, north to south.
|
|
|
|
|