If you do
NOT see the Table of Contents frame to the left of this page, then
Click here to open 'USArmyGermany'
frameset |
13th Supply & Service Battalion
2nd Support Command
Looking for more information from military/civilian
personnel assigned to or associated with the U.S. Army
in Germany from 1945 to 1989. If you have any
stories or thoughts on the subject, please email me (webmaster ).
|
|
|
|
|
Battalion
History |
|
13rd Supply & Service Bn DUI |
|
1977 |
(Source: Quartermaster Foundation website accessed July 15, 2011) |
Headquarters and Headquarters Company, 13th Supply & Service Battalion, was activated on 21 October 1977 in Germany |
|
|
1981 |
(Source: Email from Bruce L. Woodbury, former CO of the 229th S&S Company, 1980-1982) |
I found your site when I did a Yahoo search for the 13th S&S Bn. I don't know how old this site is or whether you are still interested in information. If so ...
I commanded the 229th Supply & Service Company (Augsburg) from Nov 1980 to Mar 1982. I was in command when the 13th moved it's headquarters from Augsburg to Ludwigsburg.
I was interested to see your site because of the indication that a GS supply company was formed to handle all the PSPs in VII Corps. When I commanded the 229th, the Battalion units consisted of: |
|
UNIT DESIGNATION |
DUTY STATION |
COMMENTS |
HHC, 13th S&S Bn |
Augsburg, then Ludwigsburg |
|
226th S&S Co |
Ludwigsburg |
|
229th S&S Co |
Augsburg |
satellite site in Ulm |
240th S&S Co |
Fuerth |
|
493rd S&S Co |
Wurzburg |
|
496th Supply Co (Repair Parts) |
Ludwigsburg |
|
|
|
|
|
As non-divisional S&S companies, we were not staffed or equiped to do the job of a GS Supply Company, but we still had the mission. I'm glad someone at Corps finally got wise and authorized a GS company. The Battalion was a subordinate unit of the 7th Area Support Group, 2nd Support Command (Corps). Before I took command of the 229th, I was on the Support Command staff as the Subsistence Officer in ACofS, Materiel.
If you are interested, I can dredge up more information.
229th Supply & Service Company Lineage
The 229th Supply & Service Company was constituted in January 1941 as the 229th Quartermaster Company and was activated in June 1941 at Camp Bowie, Texas. In April 1942 the company was redesignated as a Quartermaster Salvage Collecting Company, serving proudly in Normandy, the Rhineland and Central Europe. The company waswas inactivated upon its return to CONUS in march 1946, at Camp Kilmer, New Jersey. In July 1966, the company was redesignated the 229th Supply & Service Company and activated in Vietnam. While in Vietnam, the 229th was awarded the Meritorious Unit citation for its outstanding achievements during that conflict. The Company was again inactivated in December 1971 in vietnam and then reactivated in December 1972 in the Federal Republic of Germany.
229th Supply & Service Company Mission (in Germany)
The 229th Supply & Service Company has the mission to provide logistical support for all of Southern Bavaria in Classes I, II, III, IV and VII supply. The company also provides laundry, bath, renovation, and decontamination services on an area basis. As an integral part of the peacetime mission is the task of training unit personnel in all areas while maintaining the highest state of readiness attainable for combat service support. In time of war, this organization displaces, receives REFORGER elements and continues its current mission of support while assuming Graves Registration and Bakery Support elements.
The 229th wartime mission was to provide the above support to all non-divisional units operating or passing through the VII Corps rear area (and to the Corps HQ itself).
The 226th, 240th, and 493rd had the mission to provide support to non-divisional units operating in or passing through the three divisional areas of VII Corps.
I hope this helps.
BRUCE L. WOODBURY |
|
|
If you have more
information on the history or organization of the 13th S&S Bn, please
contact me. |
|
 |
|
75th GS Supply Company |
|
(Source: JOBBER, March 30, 1987) |
75th Supply 'Going through them changes'
by Robert Mitchem
"Major changes" is the phrase that best describes what has been happening at the 75th General Support Supply Company, 13th Supply and Services Battalion, since October of last year.
Since that time, the company has been through a change of command and a change in their Table of Organization and Equipment (TO&E). The realignment of the company's TO&E brought a major change in its mission, a change in work sites, a change in the number of assigned personnel, and a change in the types of equipment. The company no longer resembles, even remotely, the 42nd Maintenance (Classification Reclamation and Evacuation) Company that it once was.
With the transition from one type of support unit to another, especially in this degree, the officers and enlisted soldiers of the 75th have endured many hours of hard work and headaches.
As a maintenance unit, "The unit used to run a material collection and exchange platoon, a Class VII yard, a forward storage site for major assemblies, several pre-stock points, an automotive maintenance section, a services section, carpentry shop, a recovery and transport section, and it handled a special mission called `Operation Ziplock'," said Capt. Bruce Creamer, company commander. "Just about all of those missions have been turned over to the 317th Maintenance Company (71 st Maintenance Battalion). The company's mission now, is the running of 19 prestock points, he said.
Consequently, the occupational specialties of company personnel adjusted to reflect the change from a maintenance company to that of a warehousing unit. And the assigned equipment changed to reflect the same mission requirements. Gone are the trucks, recovery vehicles and special shop kits of the 42nd Maint. Co. They've been replaced by, primarily, forklifts.
"In October, after the second change of command, we moved all of our equipment from the motor pools and bay areas into this warehouse and the parking lot out back because we lost control of our other facilities in the change," said Ist Lt. Lydia Gurley, company property book officer. "This building was full, from wall to wall and floor to ceiling, with outgoing equipment when we started," she said, gesturing towards the ceiling of her recently renovated warehouse.
Gurley explained that the warehouse and parking lot had contained whole, parts or equipment belonging to three heavy equipment transports, two M88 wreckers, several five-ton tractors, 13 two-and-a-half ton trucks, dozens of trailers, a fuel tanker, and a jeep. There were also OVM and cock sets, test equipment, welding equipment, and carpentry material' all which had to be processed in and eventually out of the facility. And in the middle of that, a civilian contractor was renovating the facility, causing more adjustments.
"This job has called for a lot of shifting, storing of equipment, shifting, inventorying, and more shifting," said Gurley. "We had over 300 lines of equipment listed on five property books and all of it had to go. Now I'm down to my last property book," she added with a sigh.
While this activity was going on at the unit's warehouse, the company began establishing standard operating procedures for its new mission.
According to Creamer, the company actually acquired responsibility for the PSPs four years ago. But, at that time, there was little activity (stocks going in or out), so it was a minor part of the company's workload. "There just wasn't any volume of activity at the PSPs up to about a year ago," he said. "Then, within the last year, supplies (basically barrier material) that the Theater Army Material Management Center had ordered, starting coming in."
"We store Class I, II, IV, VII and IX items such as emergency pipeline material, MREs, machine guns, concertina wire, mine field marking kits and chemical suits," said SP4 Rite E. Shank, the material control and accounting specialist. "We are responsible for the handling of outgoing inventory and turn-in of Code H (no longer serviceable or repairable) material that we store. For instance, if barbed wire or fence posts get too rusty, we turn them in. Our battalion headquarters supplies the trucks, trailers and drivers for transshipment of materials from our central site to the other sites, while the company supplies transportation of manpower to the sites."
The challenging part of the PSP mission is that the sites are spread out all over southern Bavaria. They can be found as far north as Wuerzburg and Wertheim, as far south as Augsburg, to the west in Heilbronn and Ludwigsburg, and to the east in Nuernburg, where the company is based.
Unfortunately, as the company picked up such a dispersed responsibility, its TO&E change took away some of the transportation. "The TO&E designed for a general supply company does not fit the requirements of a company with our PSP mission," said Creamer. "The 75th is the only supply company of this configuration and mission in the VII Corps."
"It would be better if we could keep some of the trucks we are due to turn in, but they aren't on our TO&E," said CWO 2 Wayne Sumner, the company's motor vehicle repair technician. "We have a steady flow of work coming through the motor pool though, with the services and repair of the equipment at the PSPs," he said. "But at the same time, we have a lot of soldiers who aren't happy because they aren't being kept busy with warehouse work. It would be fine if all they had to handle were PSPs in the Nuernburg area, but there aren't enough of them for that."
In order to keep the soldiers occupied with the job they were trained to do, the company leadership has developed a program in which the soldiers spend time with other supply companies that have warehouses.The company has already assisted the 45th Ordnance Company, 71st Maintenance Battalion, with a 100 percent warehouse inventory, and Creamer has plans for his soldiers to continue working with other companies.
SSgt. Larne Smith, platoon sergeant of the Class I Platoon, has been coordinating with the 240th Supply and Service Company, 71st Maintenance Battalion. "I feel this is the way to go," he said. "It's a good idea and, more than that, it's good for the morale of the troops and good for the company. Everybody will benefit."
"The company has really been through some big changes since it was called the 45th Maintenance Company," said SSgt. Clifton Officer, NCOIC of the PSP records section. Officer had been the NCOIC of the Class VII activity (in the 45th) before that responsibility was turned over to the 317th Maint. Co.
"The job we were doing back then was very localized, with our business being conducted between W.O. Darby Kaseme and Johnson Barracks. Now there is more emphasis on logistics -- setting up personnel, transportation and equipment beforehand. It's been a real learning process for most of us higher ranking NCOs. I don't think it's a job any of us have been involved with before, not to mention the younger troops. Most of them are new to the Army, Germany and the system anyway. But we're learning to make it with what we have," he said. |
|
|
 |
|
226th Supply & Service Company |
|
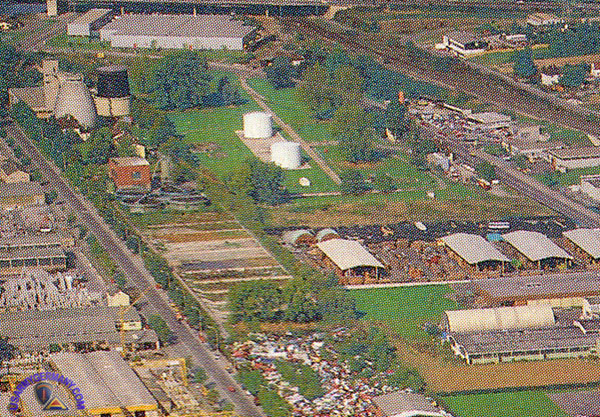
Aerial view of Neckarsulm Class III Yard in 1983 (Thomas Schulz) (Google Earth) |
|
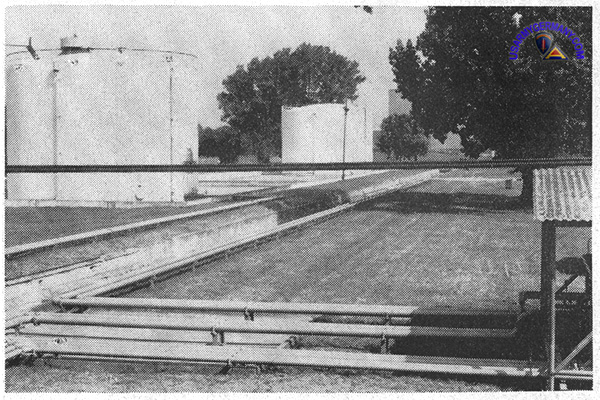
Neckarsulm Class III Yard
|
|
1986 |
(Source: JOBBER, August 11, 1986) |
When the Americans took Weinberg (Webmaster note: should this be "Weinsberg"?) in combat in 1945, they also took a Nazi POL point in the area known as Neckarsulm.
Beginning in December of 1985, the 2nd Support Command enlisted the aid of the 200th TAMMC (Theater Army Material Management Center), who sent out a PMAIT (Petroleum, Maintenance and Instruction Team) to renovate this run-down yard belonging to the 226th Supply and Service Co., 13th Supply and Service Bn. In the course of the renovation, the AMAIT team managed to modify the fuel system to accommodate two grades of product (JP/4 and Diesel) vice one grade (diesel). They installed two new pumps, filter separators and fillstands, and replaced the entire vitalic pipeline system with welded pipe. The entire system was completed and painted in early July of this year.
On July 29, the official ribbon cutting ceremony was held at the newly renovated Class III yard at Neckarsulm.
The fuel pods have a 420 thousand gallon capacity. The complete pipe system which was also reconstructed consisted of 670 meters of welded pipe.
"Words cannot say enough to thank the 200th TAMMC and PMAIT for the outstanding job they have done here," said Brig. Gen. John P. Dreska, commander of the 2nd Support Command. "They have given us a lot of dedicated hard work and consistantly outstanding support in upgrading and improving the Class III bulk fuel handling operations of the 2nd Support Command.
The 200th TAMMC has not only upgraded this yard, but have also, in the past two years, upgraded the 2nd Support Command's Hohenfels Class III yard, the Osterholz Class III yard, and the Augsburg Class III yard.
What was once rusty and old is now shiny and new, and Dreska together with the commander of the 200th TAMMC, Brig. Gen. James. E. Bickford cut the red ribbon signifying the "rebirth" of the fuel yard. |
|
|
|
1990 |
(Source: THE CHAMPION, July 4, 1990) |
DFSP Osterholz |
|
Article provides some information on the recently completed upgrade of the Defense Fuel Support Point at Osterholz (Ludwigsburg) operated by the 226th S&S Company. |
|
|
|
|
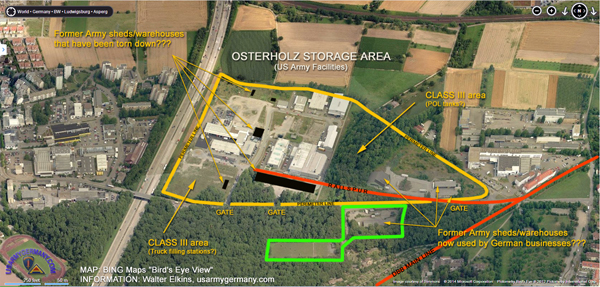
BING Maps view of the former Osterholz Class III Supply Point
(Click here for larger resolution version of image; click here to go to BING Maps) |
|
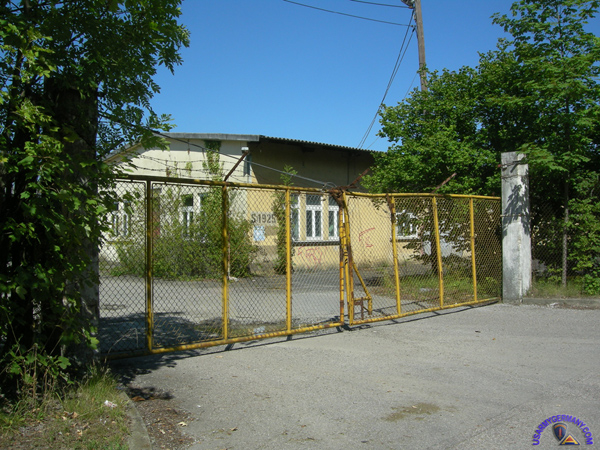
Entrance to the former filter-manifold station area (Thomas Schulz) |
|
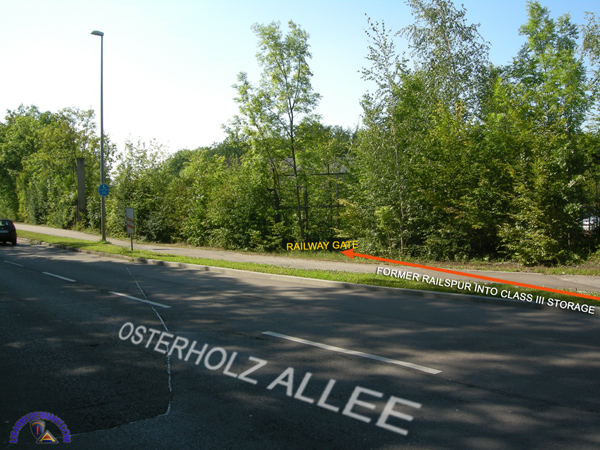
Former railway gate for access by rail tank cars (Thomas Schulz) |
|
With the help of Thomas Schulz, Germany, I have done a little research into the Osterholz Class III Supply Point which was located off of Osterholz Allee in the town of Asperg (just west of Ludwisgburg).
The aerial view (courtesy of BING Maps) gives an idea of the size and layout. However, some of the information is still speculative. Thomas was able to interview a local who remembers the facility when it was still used by the Stuttgart Military Community and was able to substantiate some of our assumptions.
The area marked with the green perimtere line was also a US Army facility but probably not directly linked with the Class III supply point.
Would like to hear from any German nationals or Army personnel who worked at any of the two facilities mentioned above or who can provide additional details. (You can use the webmaster link at the top of the page to reach me.) |
|
Osterholz Class III
Ludwigsburg |
|
|
|
|
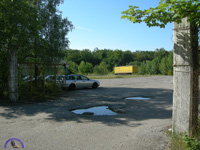
1. Entrance |
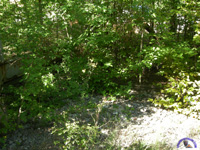
2. Railroad tracks |

3. Bldg #S1925
|
|
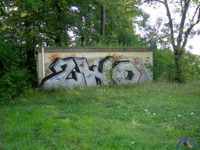
4. Transformer Bldg |
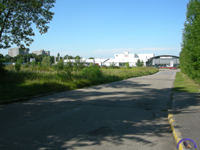
5. Former site of bulk loading station |
|
|
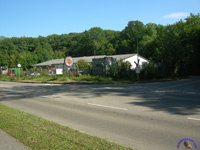
6. Unknown US Army facility |
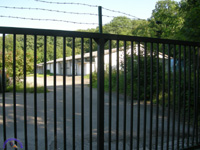
7. Close up of bldg
|
|
|
|
|
 |
|
493rd Supply & Service Company |
|
87th Maintenance Battalion |
|
1984 |
(Source: JOBBER, October 1 1984) |
493rd S&S Co |
|
Article describes the unloading of a German fuel barge by POL Platoon, 493rd S&S Co during CERTAIN FURY 84.
|
|
|
|
(Source: JOBBER, October 1 1984) |
Boxberg Fuel Depot |
|
Article provides some information on the implementation of the "emergency off-take" kit by the 493rd S&S Company to tap into the CEPS pipeline at Boxberg during an exercise. |
|
|
|
|
1989 |
(Source: Email from Bruce E. Sierra) |
I was assigned to the 493rd S&S Company from Jan 1989 - October 1991, Faulenberg Kaserne, Würzburg. We were part of the 87th Maint Battalion, 2nd COSCOM and had been for years prior.
493rd deactivated out of Ft Carson Co, rumor has it the unit is being reactivated.
At the time I was stationed on Faulenberg the 493rd was the only military unit located on the Kaserne until approx 1990 when the 3rd ID Military Police moved in to a newly refurbished building next to ours. The Civilian engineers had a large part of the Kaserne.
The Dining facility was in Building 237, the motorpool was in Building 234 and extended behind the DF and past Building 233. Our company HQ and barracks was in Building 220.
None of the "T" buildings (shown on the 1964 installation map) were on the property during my time.
Building 219 was refurbished and MP's eventually were housed there. Building 208 was also refurbished and became the Civilian Personnel Office. (CPO and the MPs had relocated from the River Building in 1990.) |
 |
|
496th Supply Company |
|
1986 |
(Source: JOBBER, October 6, 1986) |
In mid-July of this year, the 496th Supply Company, 13th Supply and Service Battalion, took on a new mission catapulting it from being a Direct Support asset of VII Corps, to a General Support asset to the Army, world-wide.
On July 14, the 107-man General Support Supply Base platoon of the 496th began operating the Army's first European Redistribution Facility (ERF) at Boeblingen Maintenance Facility, for Class IX repair parts. The basic mission of the platoon hasn't changed, it's just that they do more of it and for a bigger customer.
According to Joseph A. Bush, of the Force Modernization Office, New Cumberland Army Depot (NCAD), the development of this new supply redistribution concept and the renovation of the company's warehouse at BMF is the first step in eliminating a lone-standing excess material storage problem in USAREUR. "The ERF will serve as the Army Materiel Command's (AMC) processing and storage site for excess material primarily repair or replacement parts that are being returned by Army units in West Germany, either because they are no longer needed or have to be repaired," he said.
"All we used to do was support VII Corps. We'd take its excess Class IX and, through 800th CMMC (Corps Material Management Center) other units had access to what we had in storage," said SSgt. Elliot Cox the platoon's Transportation NCOIC. "Now we support the world with our excess through New Cumberland Army Depot." According to 1st Lt. Melanie McClure, the platoon leader, her unit's mission has gone from retail (limited resorces and limited customers) to wholesale (access to the whole Army).
Her facility has expanded in storage capacity and automation and, instead of going through 800th CMMC, she has, through Miessau Army Depot, a direct communications link-up with NCAD.
The new system has a myriad of advantages. It has reduced both transportation and procurement costs, increased the efficiency of the system, improved the limited storage capacities of USAREUR and decreased the amount of time parts remain stored at the warehouse, according to McClure.
"A high percentage of parts never hit the shelves," she said. "That's the secret of the time saving aspect. As soon as a part is processed into our Video Input Processing section we get a read-out, telling us if there is someone waiting for that component or not.
Immediately we know whether to process the part for shipment or storage. In the old process, we received parts, processed them for storage and then supplied the 800th with listings of what we had. It was then the 800th 's responsibility to match customers with our serviceable repair parts."
Time isn't the only thing the system is saving. Dale Crowell, the deputy chief of Task Force, a 13-man civilian team which is on hand to help establish the system and train the soldiers on how to run it, said that he expects the ERF to generate substantial monetary savings for the Army.
He could not estimate the dollar value, because the method for determining those figures has not yet been refined, but did note that the system has already reduced the average 'turn-around' time for parts remaining in the warehouse by an average of 66 percent. He also noted that within its first two months of operation, more than 5,900 parts of the 9000 processed into the computers had been issued. Eighteen-hundred of those orders were high priority requests.
|
|
|
|
Three months before its opening, soldiers of the 496th refurbished and outfitted the facility with enough metal and plastic shelving to alter the facilities storage capacity from 11,000 locations to over 30,000.
"One week during that time we were putting in about 15 to 16 hours a day to get this place ready," said Pvt. 1 Troy Fisher a supply specialist working in the preservation and packing section. "We worked over 100 hours that week!"
According to McClure, the rest of the refurbishing (the installing of the roller system, the laying of asphalt floors and the building of temporary bulk storage facilities) was accomplished through contracts with German firms.
"A depot level supply warehouse such as this is normally run by civilians," said McClure. "So this is excellent training and an excellent opportunity for the soldiers who may want to work at a depot on the 'outside' some day."
Sgt. Cheryl Miller, a supply specialist working in the receiving section, admitted that the job she was doing was exactly what she was taught to do in school. However, there are enough changes to make her present job seem quite different.
"We are more responsible in terms of accountability," she said. "For instance, when supplies come in we account for them by date, time, and type of carrier they came in on, such as truck or rail.
Also, the squad leaders keep track of our man hours and every section has to keep a board which tracks their production. For instance, ours accounts for how many boxes we worked on, and how many lines were in each box.
"I think we've been processing between 400 and 500 lines a day," said Miller.
"This job doesn't get boring," said Fisher. "The more I work here the more I understand, and everyone is getting cross trained into all the jobs in each section. We've even been trained and certified as customs inspectors."
October 1, the GSSB platoon's job expanded even further as it took on another class of supply: Auto Return items.
In Auto Return, chassis are refurbished, steam cleaned, body worked and painted, then returned to the system.
According to McClure two more ERFs are planned for the European Theater; one for the 21st SUPCOM and another for V Corps. |
|
 |
|
Related Links:
|
|
|
|