If you do NOT see the Table of Contents frame to the left of this page, then
Click here to open 'USArmyGermany' frameset |
Special
Troops Battalion, 2nd Support Command
Looking for more information from military/civilian
personnel assigned to or associated with the U.S. Army
in Germany from 1945 to 1989. If you have any
stories or thoughts on the subject, please contact me .
|
|
|
|
|
Special Troops Battalion
History |
|
1973 |
VII Corps DUI (worn by
personnel of STB) |
|
(Source: History
Special Troops Battalion, 1980s) |
The Special Troops
Battalion was constituted on 15 January 1973 and stationed at Nellingen,
Germany. Its mission was to establish and maintain messing and quartering
facilities for Headquarters, 2nd Support Command (Corps).
Since that time, the Special Troops Bn has added the 16th Data Processing
Unit, and the 11th and 51st Chemical Companies to give it increased
capability to support the COSCOM Headquarters.
The mission of the STB today is to provide command, control, administrative
and logistical support to the assigned and attached units, and to
provide life support and security to Headquarters, 2nd Support Command
(Corps) and VII Corps. |
 |
|
|
800th
Service Company (Corps Material Management Center) |
|
1975 |
(Source: Email from Jo Anne Jordan, 800th MMC, Dec 1975-July 1976) |
I was stationed at Nellingen Barracks (800th MMC) from December 1975 until July 1976. Wondering if the base is still in the same location in Nellingen, and if the 800th MMC is still there as a part of the 2nd Support Command.
The base was great, not too large so it was easy to find your way around. The street names were all in German.
I got married while I was there and my husband and I moved off base in the little town of Nellingen. Because of the presence of the 800th MMC there was a huge motor pool operation with trucks, tanks etc. There was a movie house on the base and lots of folks would go to the movies on the weekend. There was a very nice PX, a Catholic Church, and a great cafeteria where those living on post could go for meals.
I worked in a huge English Tudor style building that looked like a castle. The officers and other enlisted in our company would go out the windows and climb down to the ground for PT time (4-5PM). We had such a good time exercising on the lawn, running in formation, etc. I was the third WAC to ever have been in my company. Women were not a huge presence in the military when I joined and the MOS were limited. You could not be in combat.
I recall in 1975 or 76 the Bader Meinhof gang was present and we had to sit in specific areas of the base with our M-16s that we retrieved from the 2nd Support Command center and guard the area. It was really just a drill but it felt so real.
I also recall such things as being able to bargain with the locals for auto repairs on our POVs with alcohol and/or cigarattes because we could get them so much cheaper. We would have our car repaired and give them a 5th of booze or a carton of cigarettes. I remember the exchange rate in Germany (at the time they used Marks) was about 2.5 per dollar. Gasoline prices were in the upper 2-3 Marks per gallon. Living off base was fun and reazonable, although the Army gave us a cost of living allowance. I remember the town of Nellingen and the surrounding towns were pretty old - i.e. we had to light oil to heat our home. Many of the homes were heated that way. We also had big tanks above the tub and sinks that you had to turn on to get the water hot. It was quite a different lifestyle. We traveled a lot because we were given 30 days leave per year and there was so much to see and do. A lot of people would go to Mallorca, or Greece for vacation. |
|
|
1982 |
(Source: JOBBER,
November 1, 1982) |
800th CMMC:
Beans, bullets, benzine for all of VII Corps
By Robin Hawkins
Be it tanks or toilet paper, it's the 800th Corps
Material Management Center's business. If you need it,
chances are the 800th CMMC can get it for you.
The 800th CMMC's mission is to support the entire VII Corps managing
all classes of supply, (except medical and communications security
items) providing integrated supply and maintenance support.
"In plain talk, this means we perform the day-to day management to
get the beans, bullets, benzine and repair parts necessary for the
tactical units," said Lt. Col. Pete Phelan, 800th CMMC commander.
Almost all of VII Corps' support and maintenance supplies must be
requisitioned through the 800th CMMC. They are the "middle men" who
arrange for the supplies to be sent from the storage facilities or
their place of origin directly to the unit needing the supplies.
The 800th CMMC's customers are the 35 SSAs (Supply Support Activity) located throughout VII Corps. SSAs serve
VII Corps units by keeping many small supply items on hand for purchase
by units. Large scale items that the SSA does not have on hand must
be requisitioned. These requisitions are sent to the 800th CMMC for
processing.
The types of supplies the 800th CMMC deals with are many. They handle
Class I supplies, which means they make sure that the troops in the
corps have C-rations to eat in the field. They handle Class II supplies
which includes TA-50 field gear and other military clothing like fatigues.
Class III supplies, POL (Petroleum, Oil and Lubrication) supplies,
must also be requested through the 800th CMMC along with construction
items, such as concertina wire, which are considered Class IV supplies.
The 800th CMMC acquires missile munitions maintenance items and ammunition
which go under the Class V heading. They handle some Class VI personal
demand items and items known as Class VII, which includes tanks and
trucks. The repair parts for just about all these iems fall into Class
IX and the 800th CMMC can get those for you too.
"We process about a half-million transactions a year and follow up
on about 130,000 transactions a month. What we call transactions are
requests for supplies, receipt documents and follow up documents.
In terms we can all understand, last year this amounted to approximately
$230 million worth of supply requests," Phelan explained.
All the different types of items the 800th CMMC handles do not come
from the same place. Depending on the items requisitioned and depending
on the urgency of the requisition, the 800th CMMC has several places
it can turn to fill its requests.
"We have various areas we can draw (supplies) from," said Sgt. Maj.
Albert W. Dawson, 800th CMMC sergeant major.
High priority requisitions for Class II, IV, VII, IX and some Class
II items may be filled from the GSSB (General Supply Support Base) in Boeblingen. The GSSB has 18,000 different
types of items in storage and serves as the corps' back-up for supplies
during wartime and sometimes supplies urgent peacetime needs. If an
item cannot be gotten from the GSSB or is not a high priority need,
the next place the 800th CMMC would turn to acquire it would be the 200th TAMMC (Theater Army Materiel Management
Center). The final place the 800th CMMC can fill its requisitions
from are the NICPs (National Inventory
Control Point) back in the United States. There are NICPs for each
different type of supply. The NICP will pull the item from its stock
or procure it from its point of origin and send it directly to where
it is needed.
Before the 800th CMMC can fill any requisition, it first must make
sure that the unit requesting an item is authorized to have it. To
do this, the 800th CMMC's Equipment Authorization Branch keeps an
updated TOE (Table of Equipment) library. A TOE is a document that
states among other things exactly what types of equipment a unit is
authorized to have along with exactly how many pieces of each type
of equipment. Each unit in VII Corps has a TOE on file in the library.
When it is time for brand new equipment to arrive in VII Corps from
the United States, it is the responsibility of the 800th CMMC's Force
Modernization Branch to make sure that all the repair parts for the
new items are standing by ready when the new equipment arrives.
Both the Equipment Authorization Branch and the Force Modernization
Branch are part of the 800th CMMC's Logistics Support
Division. In addition, the Logistics Support Division includes
the Logistics Readiness Branch which direct the center's four commodity
divisions among other tasks. The Customer Assistance Branch supports
and assists the SSAs in making sure the VII Corps units get what they
need. The Plans and Procedures Branch is in charge of wartime plans
and policies along with planning the center's field exercises.
The center's four commodity divisions, Tank and
Auto, Missile Munitions Armament, POL and Aviation-Electronics each process the requisitions for the type of commodity they deal
with. In addition, each of the commodity divisions must keep records
on budget and monitor their overall effectiveness in meeting the needs
of VII Corps. Part of the center's mission is the concept of integrated
supply and maintenance. According to Maj. Louis Sabo, officer in charge
of the Missile Munitions Armament Division, integrated supply and
maintenance is the divisions' ability to determine on their own which
parts are needed to perform specific types of maintenance.
The 800th CMMC's Troop Support Division is slightly different from the four commodity divisions in the types
of items it deals in. Troop support manages, for the most part, the
items that the SSAs keep on hand for immediate purchase by the units.
These items include clothing, TA-50, health and comfort items, small
repair parts and other selfs-ervice items like office supplies.
The center's Systems Processing Division is responsible for scheduling the automatic data processing cycles
that are sent to the 16th Data Processing Unit, Special Troops Battalion.
The center must work hand in hand with the 16th DPU in order to process
the hundreds of requisitions that are received daily. The Systems
Processing Division must also analyze supply and maintenance systems
and evaluate their effectiveness. The division relies on their own
micro-computer terminal, the CPT-8000, to aid them in keeping track
of the mountains of data they deal with.
The 800th CMMC also maintains a word processing and IBM keypunch center
to streamline their operations.
The 800th CMMC first became recognized as a battalion in January of
this year, a relatively short time ago.
"The history of the material management center is difficult to trace
because it was initially made up by bringing together the people and
functions of several units. In a nutshell, the concept of an MMC was
started in the middle '60's but it took until the '70's to bring the
supply and maintenance functions together in VII Corps. Our unit was
basically formed when the 7th Inventory Control
Center in Karlsruhe and the Corps Agency managing maintenance
and some elements of the AC of S Supply 2nd Suppport Command were
combined at Boeblingen in 1972. Doctrine for the MMC was not formally
staffed until 1976 and it is still under development. We are very
fortunate because we have had a chance to influence the development
of our own unit," Phelan said.
The 800th CMMC's area of responsibility extends throughout the entire
VII Corps area which is north of Bamberg, east to the Austrian, Czechoslovakian
and East German borders, south to the Austrian and Swiss borders and
west of a line between Heilbronn and Aschaffenburg. The area covers
approximatey 40,000 square miles.
According to Phelan, of the five corps level material management centers
in the Army, the 800th CMMC is the smallest in terms of people.
"But I believe we are the largest in terms of transaction volume.
We definitely have the largest mission in terms of the number of troops
we support and the land area we cover," he said.
The center's authorized strength is only about 200 troops.
Phelan added, that right now a new TOE is in the planning stages for
the 800th CMMC.
"This would increase our personnel size drastically and would enable
us to do many missions that we are unable to do now. I foresee a continually
growing organization, which is the most important, logistically speaking. |
|
|
1989 |
(Source: The
Champion, Oct 25, 1989) |
Branches combined;
TAMA created
by Zena Featherston
If you need help with your tank or your missiles you'll call TAMA.
Tank, Automotive, Missile, Armament Division
of the 80tth Materiel Wanagement Center is a new division that was
created by the combination of two branches of the MMC.
Before the two branches were combined the Missile,
Munition, and Armament Branch dealt with the management
of missile readiness, munition, armament and fire control items. Munitions
was excluded from the consolidation and handled as a separate division.
The Tank Automotive Division handled
common Class IX for tanks, wheeled and tracked vehiles and major assemblies
for these systems.
The two missions interacted in certain areas. Capt. Gary M. Potts,
Deputy Division Chief, TAMA, said, "We were basically using the same
procedures in two different sections." He continued, "The concept
of merging the two sections was to facilitate more responsive support
for the VII Corps."
Under the guidance of 800th MMC Commander, Lt. Col. Patrick E. Garren,
the TAMA division was created and operational around mid-August.
Headed by Division Chief, Maj. James B. Martin and NCOIC MSgt. James
Dixon, TAMA's mission is to perform integrated materiel management
for all tank/automotive, missile and armament systems in VII Corps.
TAMA is broken down into three sections. Missile Maintenance provides
solutions to maintenance problems for missile systems. They act as
the materiel readiness manager for the missile systems in VII Corps.
They also research and validate repair parts. This section is headed
by Sgt. 1st Class Bernard L. Walker.
The Class IX Branch manages the common Class IX requisitions and processing
for applicable materiel categories. They manage the tank/automotive
portion of the GSSB stocks. And, they provide instruction on the status
for Class IX excess in VII Corps. This section is headed by Sgt. 1st
Class Shelton Davis.
The Major Assembly Branch manages the Class IX major assembly supply
of combat armament and tactical equipment in specific materiel categories.
They manage the major assembly reporting system and they prepare the
major assembly technical update. Sgt. 1st Class William W. Stites
is the NCOIC for this section.
Since the consolidation, Capt. Potts commented that the communicaton
flow was much better and in turn the customers are getting better
support. |
 |
|
|
16th
Data Processing Unit |
|
Data Processing Company, VII Corps Support Command |
|
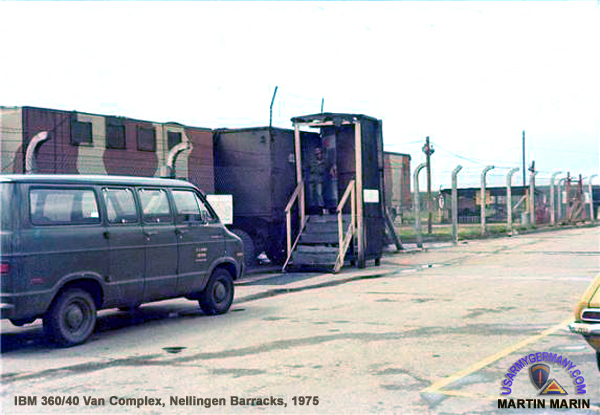
IBM 360/40 van complex after move to Nellingen Barracks, 1975. Probably in the same
configuration as originally designed by Graeme Watson and the Maintenance Team.
|
|
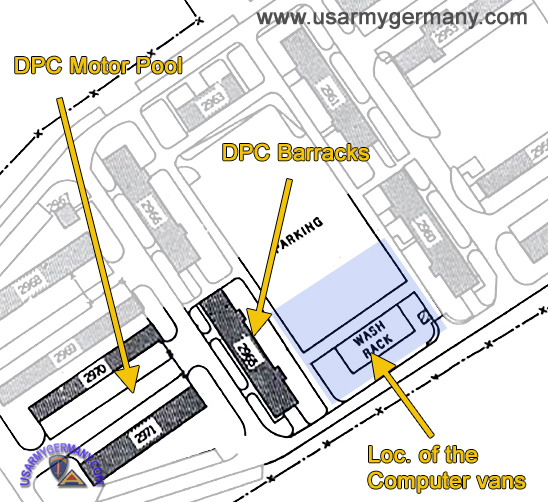
Data Processing Company areas on Panzer Kaserne, early 1970s |
|
1969 |
(Source: Email from Graeme P. Watson) |
I was a member of the Maintenance Team for the IBM 360-40 mounted in 4 trailers and parked In a lot at the rear of Panzer Kaserne.
I was a SP6 when we arrived and later promoted to SP7. My family lived on the 4th floor of Apartment 8-A-7.
I was with the maintenance team when the IBM 360 was first installed in Boeblingen. It was first shipped from the US to Gerszewki Barracks in Karlsruhe. Data files in a system there were created for the System 360.
Other expandable vans were prepared containing card preparation and processing equipment.
Three identical sets of equipment were built by IBM for V Corps, VII Corps and for use in Vietnam.
Three CWO and 9 EM were sent to several IBM schools (out of uniform) for about 9 months I had the best test scores at IBM of those who went to these classes. We were assigned to a special unit at Ft Lee (in VA).
After that training the 3 CWO selected 3 of the EM for each of their teams.
The system for Vietnam was sent to a base in California (tapes were flown there from Vietnam daily).
Th emaintenance teams, made up of 1 CWO and 3 EM's each, went to several IBM schools. Other teams of operators and support were trained elsewhere.
ADDITIONAL INFORMATION
Somewhere in my photos I have a picture taken from the 4th floor of the building adjacent to the lot where the system was installed. That is where the other members of the unit lived and worked. I will try to find the photo and scan it.
Only 4 trailers contained the computer system. It was designed for the trailers to placed side by side with a metal cat walk across the back and canvas coverings to allow the operators to move from one trailer to the other. This remained the configuration for the system installed in the yard of the IG Farben building (the system used by V Corps) until I left the Army in 1971.
The VII Corps punched card equipment was housed in trailers, which had dual AC and pull out sides. That equipment was mounted to the van floors in Karlsruhe before being taken to Panser Kaserne. We also had another A/C trailer for those who maintained and operated the four generators supplied with the system.
CWO Joseph E. Clemmons (the team leader) obtained several old dual air conditioned trailers with a side door and double doors at the rear. One of them became a replacement for the catwalk joining the computer vans. We cut holes on the sides and backed up the computer system vans to it and laid their interconnecting cables under that trailer.
Adolphos McClendon (a former SFC – now SP7) our enlisted leader was assigned to deal while the day to day operation of the team and all company related things (like KP, area inspections, etc.). I had been a SSG in Vietnam and during our schooling – now SP6.
Mr. Clemmons and I worked on positioning the equipment and getting power to the trailers. At first the generators were placed adjacent to the equipment trailers.
Across the road from Panser Kaserne where the schools and other things have now been placed, the Germans had a vast area used for tank training. We went exploring and located many long heavy duty power cables. They were sufficient to be used to extend the lines between our generators/converters to reach the equipment trailers. An engineering unit assisted in getting all of those cables moved to our site.
Their connecting plugs were useless. Mr. Clemmons ordered sufficient male and female plugs for our systems connections to the trailers. He and I along with members of the unit fabricated and installed the cables.
To keep them off the ground and prevent vehicles from driving over them, long 12” x 12” timbers were laid on the ground and the cables strapped to their tops.
I designed interconnecting corridors to go between the trailers made with 1” and ¾” plywood, 2”x4” and 2” x 6” lumber and heavy strips of foam rubber. They worked like the interconnections between railroad passenger cars. Plywood sheets were placed between the roofs of the van. 2x6's were positioned to hold other sheets hanging down the sides. Other 2x6's and a square of plywood served as a floor and was fastened to the sides. Heavy strips of foam rubber were held unto position to cover the gaps between this connection and the vans. The van doors would open and close easily. They were usually kept closed.
The computer systems interconnecting van rear door opened into a raised covered wooden platform with stairs down to the parking lot.
One of the “punch card” trailers was placed on the other side and all the other similar trailers were interconnected in the same manner.
Soon after arriving in Germany, while still in the Karlsruhe area, I went to visit a friend in a commo unit where the Germans radioed to their U-boats. He had located several rotating power convertors made during WWII to use with captured 110-220 60 cycle equipment. Upon relocating to Panser Kaserne he assisted us in installing it under a motor pool tent erected to cover the US made convertor that came with the system. It ran flawlessly. The US made converter was a horrible machine – always overheating and foaming its lubricating oil. One of those convertors was offered to be used with the V Corps system – I don’t know if they ever got
There was an IBM warehouse in Heidelberg where we could go to for parts.
The CO of the VII COSCOM DPC ws a Major.
|
|
|
1971 |
(Source: STATION LIST, 30 Sept 1971) |
DPC VII Corps Support Command, Panzer Kaserne, Boeblingen (UIC = W236AA)
DPC = Data Processing Company
|
|
|
(Source: STARS & STRIPES, May 15, 1971) |
A 13-trailer complex (within a fenced-in area on Panzer Kaserne, Boeblingen) houses the mobile IBM 360-40 digital computer used by VII COSCOM. (Webmaster note: the unit operating the computer is the Data Processing Company of VII COSCOM.)
The computer is used to keep track (in peacetime as well as in a war)
of VII COSCOM's supply and maintenance activities. To assist personnel in keeping track of supply and demand, the computer can provide up to 106 different types of reports.
A very important aspect of VII COSCOM's mission is maintenance. Monthly statistics for a typical maintenance battalion:
repair & return - 1,300 wheeled vehicles, 230 tracked vehicles, 1,900 pieces of armament, 65 aircraft, and 4,700 vehicle components;
repair parts - submission of 33,000 requests for repair parts.
One very successful procedure handled by the computer is called "cross-leveling." It can fill unit stock shortages from excess supplies held by another unit in the command.
In addition, the computer is used for keeping tabs on the 4,500 tons of ammo issued each month and a dozen other duties. |
|
|
16th Data Processing Unit |
|
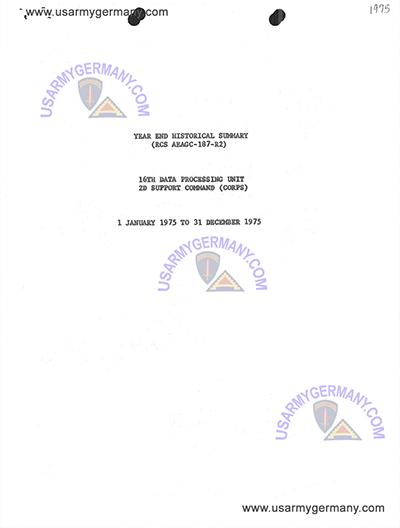
16th DPU Annual Historical Summary, CY 1975 |
|
1984 |
(Source: JOBBER,
April 9, 1984) |
A look at
computers
by Mark Heinz
Computer technology is becoming an increasingly significant factor
in our daily lives. For soldiers in the 2nd Support Command, computer
technology is more than a time-saving luxury. It's an absolute necessity.
"You have to look at our mission here which is to provide logistical
support to VII Corps," said Maj. Brian E. Harper, 2nd Supcom Data
Systems Officer. "In order to accomplish that mission, extensive automation
assets are required. Without automation, it would be physically impossible
to process the paperwork needed to get supplies to customers.
"Last year, 2nd Supcom completed more than five and a half million
supply transactions " Harper continued. This enormous workload was
processed with the help of 20 major commuter systems assigned to this
command."
Of those 20 major systems, 18 are mobile Decentralized
Automated Service Support Systems (DAS3) which are
principally located in supply support activities. All DAS3s process
supply transactions, and along with several other units within VII
Corps, feed these transactions to the 16th Data
Processing Unit. The 16th DPU completes the processing
for VII Corps and transmits the supply transactions to the theater
and CONUS. Activities such as receipts and cancellations are processed
through 16th DPU and eventually return to the customer.
Supplies which are not procured locally are ordered through the automated
supply system. A typical supply support activity orders and replenishes
several thousand lines of items that they stock for their customer,
everything from bolts for jeeps to major aircraft repair parts.
SFC Frank Pangelinan, Assistant Chief of Staff, Materiel Office, described
a typical supply transaction. "Say a unit needs a wiper blade which
they don't have in stock. They would initiate it through the Supply
Support Activity (SSA) where it would be processed through the Phoenix
or DS4 system. From there it would be transmitted to the 800th Corps
Material Management Center, who would process the requisition through
the subsystem at the 16th DPU. The requisition is then transmitted
to the appropriate National Inventory Control Point in the States,
and eventually the wiper blade is shipped to Germany, trucked to the
SSA, and issued to the customer unit.
"Once a receipt card is processed at the SSA, closing out their file,
it's sent to the 800th CMMC so they can close out their file. A typical
transaction like this usually takes between 25 and 35 days," Pangelinan
said.
To ensure that all transactions occur in a timely manner, managers
from the 800th Corps Materiel Management Center monitor all classes
of supply, with the exception of Class VIII, medical supplies. Critical
shortages are managed by the 800th CMMC, which also keeps an eye on
such things as high-dollar value items. Each class of supply has its
own manager who programs a system to block a particular item or an
item which costs over a certain amount.
While one IBM 370-138 computer at the 16th DPU is busy meeting VII
Corps' supply needs, a smaller IBM 360-40 computer is dedicated almost
entirely to supporting the personnel system.
Maj. Steven R. Edwards, 16th DPU commander, stated that, "The principal
customer that the 16th DPU supports with the IBM 360-40 is the 38th
Personnel and Administration Battalion, which services 2nd Supcom
along with all other non-divisional Corps units.
"Four Standard Installation/Division Personnel System (SIDPERS) cycles
per week are processed which insures that all personnel data such
as promotion, transfers, and reassignments are filed on the SIDPERS
data base. Each cycle runs about 10-12 hours and processes approximately
7,000 personnel transactions."
In addition to the routine maintenance of all personnel data, the
38th P & A Bn. uses SIDPERS data to obtain numerous special reports
and inquiries from the 16th DPU. This can include anything from providing
a commander with a personnel roster to determining the quantity, names
and locations of personnel with any given military occupational specialty.
Using this inquiry system, commanders can have their supporting personnel
service company provide them with a roster listing personnel according
to the commanders' needs. For example, if a commander wants to find
out which soldiers are eligible for promotion, he can request a roster
based on time in service and time in grade. The only limitations are
that they specify what information they want, and that information
is on file.
An automated system, consisting of word and data processors operating
with Wang equipment, was installed in 2nd Supcom in 1982. It provides
word- and data processing support to all 2nd Supcom chiefs of staff.
In addition to processing thousands of documents such as letters and
policies, the headquarter system has more than 80 programs that address
more than 40,000 records.
These programs manage a variety of activities for the entire headquarters,
covering minor applications such as maintaining the command group's
calendar and major applications such as the management of force modernization
for the Assistant Chief of Staff, Materiel. It provides vehicle disposition
for the Movements Control Center, and financial control for the Resource
Management office. When dates and destinations are inputted for TDY,
a program computes the projected costs.
Smaller word-and data-processing system have been installed at the
394th Transportation Battalion (AVIM) and the 6930th Civilian Support
Center. Within the next six months, 2nd Supcom's other seven battalions,
the 7th Support Group headquarters, and the 30th Medical Group will
receive similar systems. Although they are smaller than the system
in 2nd Supcom headquarters, these systems can perform many of the
same functions.
For example, the 6930th CSC recently adapted a calibration program
that was being used by the 394th Trans. Bn., keeping them from having
to develop their own calibration system from scratch. And Harper predicted
that "the sharing of data files and applications will be critical
in the future. We've already seen the need for it."
Many initiatives in the field of automation are scheduled for the
near future, to include an optical character reader, a high-speed
device capable of ingesting one page per minute. Documents such as
company SOPS may be fed into the reader, revised, and reprinted, eliminating
hours of typing.
The 242nd Chemical Company, Special Troops Battalion, is scheduled
to receive a microcomputer capable of automatically plotting fallout,
and preparing various NBC reports.
During the next year the headquarters' system, which is presently
overtaxed, should be upgraded to accommodate a system containing approximately
60 devices. (A device is a printer or terminal.) As it now stands,
the headquarters' system has 32 devices.
"Automation exists to support the users," Harper concluded. "Everything
we do in automation must be designed to meet the needs of the people
who use these tools. We're in the business of supplying answers to
needs, and for that reason automation is a never-ending process. We
must constantly be capable of adapting automation to the missions
and requirement of the Army and the 2nd Support Command. |
|
|
(Source: JOBBER,
August 19, 1985) |
Mobility is
'essential' for DPU!
by Mark Heinz
The word which best describes the 16th Data Processing
Unit is mobility. Or how about diversity.
Take your pick. The 16th DPU is a highly mobile unit whose 110 personnel
possess a wide range of military skills.
Their mission is to provide automated processing support to VII Corps
and 2nd SUPCOM personnel and logistics management missions. The majority
of this workload is handled by two IBM computer systems. Each system
occupies two 35-foot vans, while a third van houses each system's
library. |
|
|
The
smaller of the two systems, consisting of six tape drives and
nine disk drives, processes SIDPERS
transactions. The larger system processes
SAILS transactions.
Whereas SIDPERS actions deal with personnel, SAILS is a logistics
system which processes many classes of supply -- 2, 3 packaged
(4,7,8,9).
The larger computer system processes more than 530,000 SAILS
transactions monthly, therefore it's not surprising to learn
that both systems are scheduled to be replaced by a more powerful
system next summer.
"These are considered to be wartime systems," said Maj. Mark
C. Freeman, commander 16th DPU. "The reason we're in vans is
to be mobile -- to be able to processs and move. Since we're
mobile it's also important to be self-sustaining."
The 16th DPU's headquarters operates as a self-sustaining, separate
company to include a mess in the field. There are 17 different
MOS's to be found in the 16th DPU; everthing from a cook to
truck driver to a computer repairman. Organizationally, the
unit is divided into divisions to better cope with their wide-ranging
mission.
|
|
About 22 personnel belong to the Production Support Division. Their Input and Output Control section takes in raw data from customer units in the form of magnetic tapes and IBM punch cards. This data is checked for completion and verified, and instructions are added as necessary before it is sent to the Set-up and Scheduling Section.
According to 1st Lt. Lori M. Beha, Chief of Production Support Division, "Our customers tell us the jobs they need for that month, and the Set-ups and Scheduling Section schedules them into that month. In other words, they tell us what they need done, and we fit the job into what ever time slot we have available."
Also included
in the Production Support Division is the Library Section which is
responsible for managing approximately 50 disk packs and 3,500 magnetic
tapes used by the systems.
The systems are active 24 hours a day, seven days a week, and that
is the responsibility of the Operations Division. Capt. Rodrick L.
Jones, Chief of Operations Division, noted that, "We only have 25
personnel on hand even though we're authorized 43. It makes our scheduling
tough. We're short people, but the ones we have are very good, exceptionally
dedicated."
When the unit goes to the field, the systems are operated as usual.
If the customer units are not located at the field site, they may
deliver their data or a courier may pick it up.
The Programs and Systems Analysis Division performs software maintenance
of all assigned Army standard, USAREUR command and approved local
unique systems. They also provide limited software development support
to 2nd SUPCOM. CW3 Robert L. Gambert, Chief of Programs and Systems
Analysis Division, gave an example of limited software development.
"Say that the 800th Corps Materiel Management Center needs an extract
of data listing. They would send their requirements and parameters
from which to select date, and a program would be coded using executive
software programming."
Besides producing new programs, this division also fixes any problems
which might pop up in existing systems. Sp4 Charlie Vark, a computer
programmer, explained. "We have programmers who are always on call,
24 hours a day, seven days a week. If there's a problem, we have to
analyze the program. A major problem can take as long as two weeks
to straighten out."
This division's 10 personnel are currently being augmented by selected
personnel from the 167th DPU, a National Guard unit from Montgomery,
Ala. The 167th DPU had the same mission as the 16th DPU. But according
to Sp5 Sherrell E. Turner, a guardsman from Greenville, Ala., "It's
hard to get much training in two days a month." So the guardsman are
sent to train with the 16th DPU for three-week cycles.
Problems with hardware are handled by the Maintenance Division. "We
run pretty much trouble-free," said SFC William R. Brown, senior automated
repair supervisor. "Less than one percent of the total available time
lost is due to hardware problems. As far as the basic computer systems
go, we lose very little time."
Preventive maintenance is pulled weekly on both major IBM systems
and the autocom, and periphereal systems such as key punches, paper
separaters, and tape testers.
CW2 Terry Corbin, Chief of Maintenance Division, said, "We're the
most diverse division in the 16th DPU because of our different missions
and MOS.
"We have two distinct missions. One is the support of computer systems
up through depot-level maintenance. The other is the maintenance of
the 55 vehicles in our motor pool."
The Maintenance Division also maintains the unit's huge 100-killowatt
generators and its air conditioners.
According to SSG Edward Velez, a utility equipment repairman, "During
our last field problem we had an electric source available and we
had a converter, but we used the generators as something new. After
all, that's what we might have to rely on at a remote field site."
|
|
|
1986 |
(Source: Email from James Martin, 16th DPU, 1986-88) |
I was stationed at the 16th DPU in June of 1986 to about June of 1988.
I wore the "Excell All" pin and the silver sword on blue background.
My MOS was 74 Foxtrot, i.e. computer programmer.
Shortly after I showed up the old IBM 360's were replaced by 2 IBM 430's (sic), which proved be better machines. They were still trailer mounted, and while I was stationed there we went on two training exercises.
When I arrived, there were about 110 people in the 16th. When I left there were only about 40 people, and we were still doing the same job running SIDPERS, which I forgot about until I read it in your site.
This was an amazing time for me in the service. I remember working for Major Freemen -- he was fair, straightforward, and he cared about his troops. He was very good at keeping his troops from being sent to do other unrelated duties, such as working at the guard shack.
I still remember a few of the names of the personnel stationed there. I remember working for CW3 Robert L. Gambert. He was a marathon and triathlon runner. He made us young kids look wimpy when we went on our weekly / daily runs. Sp4 Charlie Vark had just shipped out before I showed up in Nellingen, so I heard about what a great programmer he was, but I didn't know him.
I wish I knew where some of these people are now. Do you know any of them from 1986 to 1988?
I later spoke with SP4 Scott Alves, who worked with me at the 16th. He said that when he was working in the MP detachment during the first gulf war he spotted the 16th DPU trailers in the distance.
|
 |
|
|
229th Trans Co (Movement Control Center) |
|
1987 |
(Source: JOBBER, April 27, 1987) |
229th MCT No. 2 in USAREUR NDTA
by Robert Mitchem
First they took 2nd Support Command (Corps).
Then they took VII Corps. And soon after that,
the Movement Control Team, Stuttgart, 229th
Movement Control Center, made an excellent showing
at the USAREUR-level National Defense
Transportation Association competition, finishing
with first place in its category and second overall.
As part of their day-to-day job, the MCT is responsible for controlling all movement of cargo within the Greater Stuttgart Military Community. |
|
|
According to Lt. Col. Curtis Houston, ACofS, Transportation, the 229th MCT has commitment authority over units such as the 4th Transportation Battalion. That is, when a truck from that battalion hits the road, it must first be cleared through the MCT.
"They oversee and arrange transportation of cargo, not only by truck, but sometimes by CH-47 Chinook, commercial rail and occasionally by certain theater assets," Houston said.
"For instance, if the 3rd Infantry Division should need to get something to Crete, Greece, the 229th MCT may arrange for the Air Force to do the lifting.
The NDTA is a world-wide competition, and the next level following USAREUR level is the national competition at Headquarters, Department of the Army. Unfortunately for the 229th MCT the competition is run differently at that level.
According to Houston, while USAREUR's Deputy Chief of Staff for Logistics looks for the best unit in three different categories, the national competition focuses on the one best transportation unit Army-wide.
USAREUR is allowed only one nominee in the national competition, yet different types of organizations compete in separate categories at USAREUR-level, Houston added.
|
|
The three USAREUR-level categories are:
 Trucks. Motor transportation or aviation;
 Installation Transportation Offices, dealing with personal property; and
 Movement Control Units. Those who deal essentially with freight or unit moves. The 229th MCT fell under this category.
Houston said that units in Category 1, trucks, are usually selected to represent USAREUR at the national level, because that is the type of unit DA is looking for. The 15th Transportation Company, 4th Transportation Battalion, was 2nd SUPCOM's nomineee to the category, and made it to the USAREUR competition. However, it didn't place high enough at USAREUR to continue on to DA-level.
Every soldier in the 229th MCT does not belong to 2nd SUPCOM. About 80 percent of them are from the 39th Transportation Company, 4th Transportation Command. They are, however, attached and under the operational control of 2nd SUPCOM.
"Their Table of Organization and Equipment belongs to the 39th," said Houston, "but they are attached to us, and their major's report card comes from 2nd SUPCOM."
Lt. Gen. (Ret.) Oren Dehaven, the honorary Colonel of the Transportation Regiment, presented the 229th MCT with its award during the NDTA European Conference held April 14 in Munich. |
|
|
(Source: JOBBER, May 11, 1987) |
`Nothing moves it we don't do our job'
by Anna K. Van Note
Hundreds of soldiers and family members in the 2nd Support Command visit the Nellingen American Express Banking Office every day, but few people realize what crucial work is taking place underneath their feet.
Downstairs, past the Craft Shop, in
the very back of the basement of
building 3503, is the headquarters of the
VII (U.S.) Corps Movement Control
Center. It is small in size when measured
against other battalions in the command,
but it has a very challenging mission.
"Briefly stated, our mission is to provide effective transportation movement management for all commercial container, highway, Army and Air Force air, rail and inland water operations supporting VII Corps," says Maj. Thomas R. Clark III, a 1973 Virginia Military Institute graduate who serves as the MCC executive officer. "The MCC works closely with the Material Management Center to arrange movement of all classes of supply (except bulk POL by pipeline) within, into and out of the VII Corps area."
The MCC is comprised of several elements. |
|
|
The Highway Traffic Headquarters (HTH), led by Maj. Harland M. Borneman Jr., receives and processes all convoy clearances and road movements bids for VII Corps units, as well as other units which pass through VII Corps boundaries.
The HTH plays one of the most critical roles in German-American military liaison in the VII Corps. Every major U.S. convoy element on German roads in the Corps area must be processed by the HTH and their counterpart, the Verkehrskommandaturen (Verrk). The Verrk offices use a computer system to track all convoy movements in West Germany.
|
|
The daily operations mission for the MCC is handled by the Movement Control Element (MCE). The soldiers in the MCE manage the transportation needs for the entire VII Corps, taking customer requests for transportation and determining how to best move the cargo -- by truck or train, or by air.
"The commitment process works like this," explains SFC Richard J. Rieks, the MCE NCOIC. "Let's say a unit has some cargo or equipment which needs to be moved. They call one of our Branch Movement Control Teams (BMCT) and provide a description of the cargo, a pick up and drop off location, and request a move date. The BMCT passes the request to its Movement Control Team (MCT) in either Nuernberg or Stuttgart. MCTs serve customers on an area basis.
"Then the MCT calls me or one of my soldiers at the MCC for a control number," he continued. "That number tells the transportation unit, like 4th Trans. Battalion, that I have approved the commitment. Fourth Trans. then determines which truck company will support the tasking. We do more than just manage the truck commitments, though. We handle all the air and rail requests, and track container and MILVAN management, and set up HET (Heavy Equipment Transport) move, too."
The MCC has 22 subordinate movement control elements. The two Movement Control Teams in Nuemberg and Stuttgart each have six to eight Branch Movement Control Teams, which are staffed primarily by local national employees. Additionally, at the Center headquarters at Nellingen, the MCC is served by a plans and exercises section, as well as detachment headquarters, which provides limited logistical support to the MCC.
"I command one of the most diverse units in the entire VII Corps, both in geographic location and mission," says Lt. Col. Tommy W. Vassaur, MCC commander. "I would not trade this experience for any other command. We are the transportation managers for this Corps. Nothing moves if we don't do our job. To be most effective, our traffic managers must not only understand transportation principles and procedures, but also must possesss a solid background in supply and maintenance support operations and unit movements by surface and air transport modes."
(1st Lt. Anna K. Van Note is the adjutant for the 229th Movement Control Center). |
 |
|
|
353rd Quartermaster Parachute Packing Detachment |
|
1974 |
(Source: USAREUR STATION LIST 1 July 1974) |
The 353rd QM Parachute Packing Det is located at Storck Barracks, Illesheim. |
|
|
1975 |
(Source: Army Heritage and Education Center archives) |
, AHR 1975 - AHEC 400.jpg)
1975 Annual Historical Supplement, 353rd QM Det (AHEC) |
|
 |
|
|
Related Links:
|
|
|
|
|
|