If you do
NOT see the Table of Contents frame to the left of this page, then
Click here to open 'USArmyGermany'
frameset |
Computer Systems Command Support Group Europe
US Army Computer Systems Command
Looking for more information from military/civilian
personnel assigned to or associated with the U.S. Army
in Germany from 1945 to 1989. If you have any
stories or thoughts on the subject, please contact me .
|
|
|
|
|
Computer Systems Command Support Group Europe History |
|
1969 - 1985 |
(Source:
Department of the Army Historical Summary: FY 1969) |
The increasing development and installation of automatic data processing systems to support functional applications that may be similar in two or more major Army commands raised a need for better central planning and control. To satisfy that need, the U.S. Army Computer Systems Command (USACSC) was activated at Fort Belvoir, Virginia, on March 31, 1969. The command was designated a class II activity under the jurisdiction of the Assistant Vice Chief of Staff. It was assigned responsibility for development, installation, improvement, and other related support functions for Army multicommand automatic data processing systems, and will perform project management for assigned systems in response to functional requirements formulated by headquarters staff agencies. The command will insure effective communications planning and support for such systems and will conduct software research programs in co-ordination with the Chief of Research and Development.
Late in fiscal year 1968 the Directorate of Management Information Systems in the Office of the Assistant Vice Chief of Staff completed a study which revealed that certain organizational realignments at Headquarters, Department of the Army, level would benefit the Army's approach to information systems design and promote a more effective use of automatic data processing equipment. Thus in July 1968 the responsibilities assigned to the Director of Automatic Data Processing in the Office of the Comptroller of the Army were transferred to the management information systems directorate, including jurisdiction over the Computer Systems Evaluation Command. The latter was redesignated as the Computer Systems Support and Evaluation Command and was made a class II activity under the directorate. As a result of this realignment, the management information systems directorate is now able to monitor, on an Army-wide basis, the design of information systems and the use of associated automatic data processing equipment. The directorate also has the professional capability to evaluate and select computers for all elements of the Army and provide a single point of contact with industry in this field.
|
|
|
1970 |
(Source: STARS & STRIPES, April 4, 1970) |
(In April,) US Army Computer Systems Comd (CSC) at Ft. Belvoir, Va, added the Theater Army Support Command (Supply) (TASCOM(S)) data system to its inventory of multi-command data systems that it supports.
TASCOM(S) was developed by Material Command Europe (a subordinate command of TASCOM) and provides centralized theater control of supply management, stock control, field depot maintenance, and supporting finance and transportation functions.
The above change also saw a transfer of 91 personnel (US military, DAC and local nationals) from the TASCOM(S) project in Zweibruecken to the CSC's new field agency, also located at Kreuzberg Ksn in Zweibruecken. |
|
|
(Source: STARS & STRIPES, June 23, 1970) |
US Army Computer Systems Command, Europe
The mission of USACSCE is to provide assistance in the installation, maintenance, systems design and programming of computers used in logistical support of US Army, Europe. CO of USACSCE is Col. Paul Autrey.
137 of the worldwide 1,100 personnel of USASCS are assigned to the European element of the command. With headquarters in Heidelberg, USACSCE also operates two field offices, the Karlsruhe Field Agency and the Zweibrücken Field Agency (Kreuzberg Ksn).
On July 1, 1970, TASCOM's computer system (Materiel Command, Europe) came under the jurisdiction of CSCE and is now the Zweibrücken Field Agency. The Agency is responsible for the design of programs, programming and maintenance of MATCOM's computer complex at Kreuzerg Ksn. The Agency's personnel (Army personnel, DA Civilans and Local Nationals) are divided into three levels of assignment -- systems analysts, computer programmers and computer specialists. The computer complex at MATCOM keeps current records on supplies within the Theater - materials on hand at depots, materials arriving from CONUS depots, supply movements within the Theater, and a list of available parts in the Federal Catalog. (Webmaster note: the computer complex includes the IBM Systems 360/Model 50 mainframe computer.)
The Karlsruhe Field Agency provides guidance for computers used by the five combat divisions within USAREUR as well as 41 smaller military units. The Agency has similar responsibilies as the Zweibrücken Agency, supporting two different computers. Personnel of the Karlsruhe Agency must travel to several operational installations throughout Germany as well as assist in preparations for smaller systems still in the installation phase. They are on call seven days a week and when called for onsite support can be away from the home office for up to two weeks or so.
The combat divisions use the mobile UNIVAC 1005 card processor (developed for use by divisional support units) utilizing the DELOGS (Divisional Logistics System) program for Class IX supply. The non-divisional DSU-GSU combat service support units utilize NCR-500 automatic ledger posting machines for stock control and accounting.
Prepartations for the installation of smaller computer systems includes personnel of the Karlsruhe Agency going to the unit 30 days before the arrival of the system. There they assist in getting the data placed on keypunch cards. 30 days after the computer has been installed, the team returns for a technical visit to the unit. |
|
|
1984 |
(Source: US Army Information Systems Engineering Command website) |
On 15 May 1984, the United States Army Communications Command (USACC), a major command (MACOM) of the U.S. Army, was redesignated the United States Army Information Systems Command (USAISC). It was given the mission to manage the Information Mission Area (IMA), which was to place the responsibility for all areas of information management within the U.S. Army under one command. On the same date, the U.S. Army Computer Systems Command (USACSC), a field operating activity of the Headquarters, Department of the Army Assistant Deputy Chief of Staff for Operations-Command, Control, Communications, and Computers (C4), located at Fort Belvoir, Virginia, was transferred to the USAISC as a major subordinate command (MSC). Both of these actions were authorized by Department of the Army General Order No. 26, dated 25 July 1984.
On 1 October 1984, the USACSC was redesignated the U.S. Army Information Systems Software Support Command (USAISSSC) by USAISC Permanent Orders 42-1, dated 14 September 1984. Nine months later, the USAISSSC was redesignated the U.S. Army Information Systems Engineering Command (USAISEC) by USAISC Permanent Order 79-1, dated 1 July 85, and has retained this designation to the present day. |
|
|
(Source: Email from John W. Fleming, USACSC-SGE, 1978-82) |
I was stationed with the US Army Computer Systems Command from 1978 to 1982 at Kreuzburg Kaserne, Zweibrücken. The CSC unit in Zweibrücken was the USACSC-SGE (for Support Group Europe). There was also an Support Group Lee (SGL) and a Support Group Pacific (SGP). Back then we 74series were still AG.
I was with the 66th MI Brigade from 1987 to 1989 at McGraw Kaserne, Munich. Your web site has brought back many good memories.
USA Computer Systems Command The following is a synopsis of the Computer Systems Command as I remember. Time has obscured some of my memories. My capacity at the time was that of a trouble shooter and analyst. All the major STAMMIS (Standard Army Multi-Command Management Information Systems) programmers and management personnel for financial and personnel systems were located at Fort Belvoir, Virginia. Other stateside posts had responsible programmers and managers for their specific areas of interest. The Intelligence community was supported by elements in Munich and Augsburg and the communications community was located in Worms. CSC was originally based in France prior to its movement to Kreuzburg Kaserne, Zweibrücken FRG in the 1960's. I arrived in March 1978. At that time most CSC personnel were situated in building 4001. There were two computer centers, one in building 4003 (two IBM system 360-70's back to back). The other was located in building 4008, a larger main frame IBM computer system which, I believe, later replaced the one in bldg 4003.
The primary mission of the CSC was to provide operational and system support to DA Standard Management Information Systems and USAREUR unique systems. Among the DA STAMMIS systems were civilian and military personnel accountability systems, finance and accounting systems, logistics systems, and training management systems. I was primary on SIDPERS, TUFMIS, and ASAC (Automated Systems Army Commissaries - a commissary management system which was enlarged from a small stateside program to support all European commissaries. It was a programming nightmare and loving known as "A Sack of S----"). I was also back up on STANFINS (Standard Army Financial System), STARCIPS (Standard Army Civilian Pay System), DLOGS (Defense Logistics System) which was later modified to run Honeywell mini computers at Division level (the
DAS3
systems).
The main location of my primary systems were located in division level mobile operations centers called CS3 vans, (Combat Service Support Systems). These were van mounted IBM system 360-40's. Primarily these were configured in three or four van setups: a processing van with the CPU, card reader and card punch machine; the mass storage van with tape and disk drives; a supply and storage van; and an analyst van with desk and reference manuals. They were supposed to be mobile and easily set up and operational, but half the time it took the whole exercise to get them up and running after they were moved. As trouble shooters we spent almost all out tour going TDY to the various divisions and Corps to resolve processing problems and to implement change packages (SCPs) when forwarded by the STAMMIS programmers.
|
|
If you have more
information on the history or organization of the USACSC-SGE or ISEC-EUR, please contact me . |
|
|
(Source: USACSC-SGE phone list is from the USAREUR Telephone Directory (Troop Units), 1980; explanations are provided by John Fleming) |
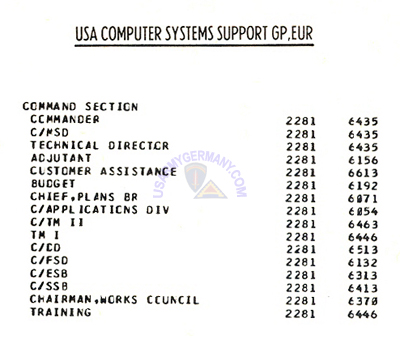
USACSC-SGE Telephone List, 1980
|
Yes, Team I and Team II, were the troubleshooters. I forget which one I was (Team II I think). I don't know why but the Chief/TM II was also the Chief of TM I. One of my favorites was Cpt. Elaine Godzack.
And I believe it was Chief/Management (or Maintenance?) Support Division (Records and Tech Library). I can't remember his name, but I have a picture of him at a party in France. If he's running for public office, I'll print it. One of the branches was the OMD (Operations Management Division), the technical library.
I'm not sure about C/CD. There was a C/OD, Chief/Operations Division. Mr. Donald D. Kampen was the boss. (Webmaster Note: after loking at the print with a magnifying glas, I would agree that the correct designation in the telephone directory was C/OD.)
Chief/Field Support Division. Mr. Steven A. Ward was one of the bosses during my tenure.
|
|
Ms. Levitta Liggins was the boss of the European Unique systems but I'm not sure which division she fell under.
And of course, Chief/ Standard Systems Branch; the STAMMIS folk. Mr. Bill Garner was my boss, and one of the best bosses I ever had.
Also, C/ESB was Chief/Executive Software Branch, the OS (Operating Systems) and DOS (Disk Operating Systems) guru's. My good buddy, Sgt Brian Murphy used to go TDY with me to resolve JCL (Job Control Language) problems. Usually Corps level computers ran the OS systems as it was a little more complex than DOS. DOS was run mostly at the division level. In the early 1980's when more powerful IBM systems came into being, OS and DOS pretty much fell by the wayside.
Maybe this will stir memories from other members, if there are still some around.
|
|
|
(Source: INTERFACE, US Army Computer Systems Command newsletter, February 1981) |
SGE: Ready for action
By John H. Sanders
Approximately 350 miles from Berlin and 1350 miles from Moscow lies the United States
Army Computer Systems Command's
(USACSC) Support Group Europe (SGE).
Located on Kreuzberg Kaserne in Zweibrucken,
West Germany, SGE has the responsibility of
insuring that the overall mission of USACSC is
effectively carried out in the European theater.
"Our role is primarily that of support," said
Col. Oliver W. Hedges, SGE's Commander. "We support all the ADP users in Europe that utilize
USACSC products to include both our own
unique products and the products that are put out by the command headquarters.
"We do this both in a peacetime mode on a
day to day basis, but always, at the same time,
ready to converge and get into a wartime
posture if necessary. Because we arc here, near
the forward edge, all of our work has to be undertaken with the thought that we could be in wartime posture at anytime. This is the way we operate and do our job, ready to transition to war at the drop of a hat."
At first glance, one realizes that SGE is strikingly different than most facets of USACSC. All soldiers are in fatigues, and field gear and weapons are only an arm's reach from the soldier's desk.
|
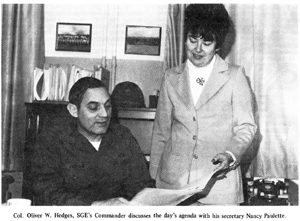
Col Oliver W. Hedges, SGE's commander, discusses the day's agenda with his secretary, Nancy Paulette
|
"Everyone knows what they've got to do should the balloon go up," says Hedges. "And they're ready to move out, live in a field environment, and support command software."
During peacetime, SGE is, of course, under the command and control of USACSC Headquarters. However, in the event of war, the Commander in chief of U.S. Army Europe (USAREUR) would assume operational control. In such a case SGE would be liaison to and coordinator with the HQ USAREUR staff, it's major subordinate commands, and their data processing installations to include functional users of ADP systems operating in the European Theater for which USACSC is the Assigned Responsible Agency (ARA).
|
|
Here in Europe, we are the Computer Systems Command, Hedges said. We wear the patch and we fly the flag. So when anyone in
Europe wants to talk about a CSC problem, let's say, we're the people they call. All calls and requests for assistance from Europe come here, even if the question is posed to the headquarters or another support group. In many cases we are able to resolve the problem here without having to go back to the headquarters or another support group. So in this respect, we are totally cognizant of what the headquarters is doing.
DOES ANYONE KNOW WE'RE HERE?
When asked if he felt that the European Theater was aware of SGE's presence, Hedges quickly replied, "The command structure is very much aware of our presence here. We attend many of the major briefs at USAREUR Headquarters and have many discussions with the Deputy Commander in Chief, USAREUR concerning the ADP community. I know that the command and most of the commanders are certainly aware of SGE's presence, and there's no question that the ADP community in Europe is totally aware and highly supportive of what we do here in the European Theater."
Twenty-nine military, 27 Department of the Army Civilians (DAC's) and 25 German nationals comprise SGE's workforce. Is it difficult for a commander to be the boss of three very distinct work forces? No, all my people are sharp and number I in my book, but it is a challenge, says Hedges. All three work forces have their own aspirations and their own set of rules and by-laws. The green-suiters know that they are on call 24-hours a day seven days a week. Being one myself I'm very familiar with how we operate and what is expected, he said. (Hedges has over twenty-two years in the military.) I also have had much experience working with DAC's, here and in CONUS where I had been the IG (Inspector General) for USACSC for three years before coming here six months ago. The DAC's that I have here are a real dedicated group of people. They are certainly willing to put in all the time that's needed to get the job done and then some. Of course, their rules and regulations concerning overtime, leave and so forth are different than those of the military but I really don't have any difficulties working with them at all.
Working with the German nationals has also been a treat for me in the sense that they are very hard workers and enjoy working with us. They definitely complete our team. However, they also have their own rules for doing things. They are all part of the German Works Council which is something similar to a labor union. Simply put, no changes of any sort can be made without the council's
approval. Nothing can be done whether it be an organizational change, or the changing of work hours. Anything that could affect management must be coordinated with the local German Work's Council. That's the rule. Fortunately I have a very good relationship with my Works Council. I certainly keep very close relations with them. And they're very good people. I guess the bottom line for me is that I must always remember that every decision I make may affect the total work force in three different ways.
WHY IS SGE IN ZWEIBRUCKEN?
In 1969 when USACSC was formed, and the support group in Europe was made a part of the command. It was divided into a headquarters element and two field agencies. The headquarters was at Heidelberg and the field agencies eere at Karlsruhe and Zweibrucken.
|
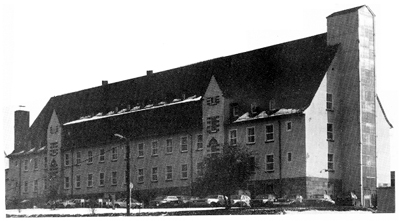
SGE Headquarters, Kreuzberg Kaserne, Zweibrücken
|
According to Hedges there became a need to amalgamate and consolidate the three as they accepted more and more of the central design of all of the European systems. It was decided that they simply couldn't be the central design agency being split in three parts, so the decision was made to bring all the resources and all the talent under one roof. But, what roof? Heidelberg's and Karlsruhe's location were too small to house the 200 member work force. Thus, SGE was brought together under one roof at Zweibrucken.
|
|
Certainly it probably would be better for us to be located in the Heidelberg area, Hedges said, because when we go out to all four corners of West Germany and Europe, being down here in the southwest corner -- so to speak -- does not facilitate our travel. But, that doesn't mean we don't like Zweibrucken, because I'm sure there's not a soul that wouldn't rather be here than Heidelberg. It's very nice here and it's a great community. The people here treat the military like kings and I think it's one of the very fiew communities in Germany that will really say they like the American soldier or the American presence. You can go downtown and people are very outgoing, very friendly and they'll bend over backwards to do anything they can for you. The people here, I know, would just rather be here than anywhere in Germany because of this relationship.
MAXIMUM UTILIZATION OF RESOURCES
Last summer, SGE reorganized, according to Hedges, "To get maximum utilization from our resources."
"We're going through the growing stages of making this reorganization work, of interfacing with each other, establishing the correct lines of communications and we're doing it basically with the guidance given to us by command headquarters to insure that we have more quality assurance," Hedges said.
He also said that from what he saw, the reorganization was coming together well. And that he was excited about it.
"I think our people are communicating better and we're becoming a more cohesive organization by the fact that we have undergone this reorganization. I think it will be a big plus in the way we do business and the way we provide support to the field. I also believe we're going to provide better support with better understanding.
Hedges' philosophy concerning work is that, "We need to develop our jobs and we need to develop our organization with the thought of enjoying ourselves - maybe even to the point of having fun. I believe you have to enjoy the work you do, have fun at what you're doing, enjoy the atmosphere and work toward that end. I think that if you have this attitude -- no matter what you do -- you're going to produce better results and have a happier group of people, one that is a heck of a lot more responsive. If you don't enjoy what you're doing let's find out why and get the things that are bothering you out and make it enjoyable."
Hedges gets together with the entire support group once a month for awards and promotions, however, he doesn't stop there. He takes time to tell them where they've been, where they are and where they're going and gives them all a pat on the back for their efforts. He's out to make his support group the very best. |
|
The Mission of Support Group Europe
Provides the interface with and communications link between USACSC CONUS based Application System Developers for Standard Army Multicommand Management Information Systems (STAMMIS) and USAREUR based functional users of and USAREUR DPI/DDC's operating these systems.
As directed by CG, USACSC, acts as Application System Developer (ASD) for USAREUR Standard ADP Systems. The ASD functions include detailed ADP technical system design, systems analysis, computer programing, program and system testing, technical documentation and fielding during the development, installation, and maintenance phases of the life cycle. The basis of operations is according to the Memorandum of Understanding (MOU) between CINC USAREUR and CG USACSC, and a supporting Letter of Agreement (LOA).
Assist and support the installation of USACSC Standard Executive Software needed by USAREUR DPI/DDC's for operation of STAMMIS and USAREUR Standard Systems. Generate, install and support such USAREUR Standard Executive Software which cannot be accommodated by USACSC Standard Executive Software.
Provides systems conversion and extension support for new STAMMIS introduced into USAREUR and for existing STAMMIS onto new or upgraded Automatic Data Processing Equipment (ADPE).
Provides technical field support to USAREUR functional staffs and users, Automation Management Officers (AMOs), and DPI/DDCs for fielded STAMMIS, USAREUR Standard Systems and supporting executive software; including system problem identification, coordination and resolution; technical support visits to assist functional users and DPI with system training; assistance with the DA and USAREUR ADP Standardization Program; and other general ADP assistance.
As a representative of the centralized Army Developer of STAMMIS and USAREUR Standard Systems ASD, provide other general ADP assistance to, and answer questions from USAREUR functional staffs and users and to DPI operations and programing staffs. (This assistance is provided over and above Incident Report or System Change Request Channels and includes telephone questions/responses, correspondence, meetings or on site visits to provide DPI/functional user general ADP technical information and assistance to explain/clarify systems operations, content, or processes.) |
|
SGE's Customer Assistance Office |
|
(Photo on left) At SGE's Customer Assistance Office (CAO) Elizabeth Napier, Computer Technician receives an incident report from one telephone caller, while hoping to make a connection on another line to one of the 109 DPI's in Europe that the SGE services. In the background, MSgt. William H. Welch, CAO Chief, discusses information concerning a Systems Change Package with Emogene Zabel.
"Our entire function depends upon and revolves around the telephone," Welch said. "At times it is virtually impossible to get a call through. There are days when we might spend one to three hours trying to contact a particular DPI about an incident. On other occasions -- if we're fortunate enough to get through -- we hear some very bad static. Sometimes it costs us an
extra day's work. Plans for
a new telephone system, however, are in the talking stages according to Welch.
It is the CAO's responsibility to receive, record, control and dispatch assistance and follow-up action for Incident Reports initiated by DPI operators and functional users. They are also to track, record and communicate to the systems baselines in operation at the DPI serviced by USACSC. In addition, the CAO is the DPI's initial point of contact for reporting emergency or urgent problems with STAMMIS USAREUR Standard Systems, as well as supporting Executive Software Systems. They also provide communication interface between USAREUR DPI analyst/operators and SGE technical field support technicians and USACSC CONUS-based CAO's in problem solving.
|
|
|
Decentralized Automated Service Support System |
|
Decentralized Automated Service Support System (DAS 3) training classes have been established at SGE so more and more individuals will have a better understanding of the computer hardware as the DAS3's begin to roll into Europe.
Bill Garner, who has been teaching the six week course for several months tries to get a representative group of people from all directorates within SGE for a little "on the job training."
(Photo on left) Garner teaches some fundamentals of programing on the Honeywell level 6 computer inside the DAS3 van - to Harold Schimeler. (Left to Right) WO 1 Daniel Childress, MSgt. Jerry Moore, Ronald Stough and Sp6 Brian Murphy look on.
|
|
 |
|
|
ISEC-Europe History |
|
US Army Information Systems Engineering Command decal |
|
(Source: ECHO, June 1985) |
Support in war, support in peace
By Lee Royal
It started with a build-up of tensions between the East and West through conflicts elsewhere in the world. Days later, several divisions of Eastern block soldiers deployed to the East and West German border as reinforcements to Soviet divisions already in place.
Then the attack began - the eastern soldiers invaded at multiple points in Northwest Germany.
They were supported by Czechoslovakian forces in the South.
United States forces deployed to the field and maintained their positions. In the rear, 21st Support Command began working 24 hours a day to provide logistical support. Suddenly there's a breakdown in critical computer software, but the mission must go on.
That could have been a scenario for the first five-day Standard Army Multi-Command Management Information Systems (STAMMIS) Software Support Exercise.
The Information Systems Engineering Command Europe (ISEC-EUR) in Zweibrucken deployed three teams of computer programmers and analysts from the Software Directorate to the V and VII Corps and the 21st SUPCOM.
They are responsible for providing software support to USAREUR major subordinate commands in both peace and wartime missions.
An individual can't handle all the logistical requirements in today's Army without a computer, says Brian Grieser, major command team leader. As soldiers use computers more and more, they become dependent on them.
"It would be easy to lose sight of all the equipment by doing it all manually," he says. "The Army is so big and complex that we rely heavily on computers to keep track of everything."
The five to seven member teams provided total software support for the units' day-to-day missions as well as the exercise scenarios.
"We are strictly software specialists," says CWO 2 Joseph Galloni, team chief. "Every team member specializes in a certain area - like a medical specialist. One person specializes in eye problems, another on throat problems. So one person on our team specializes in Honeywell software, another on IBM software."
But handling a wartime mission is different from the peacetime mission. During the day-to-day mission, the users call the customer software assistance office in Zweibracken if they have a problem. But during the exercise, the users called the team directly at the site.
"We can handle our peacetime mission," says Sgt. Michael Danna. "I wanted to get more familiar in the field. I can do the mission - now I've had the chance to prove it."
There were many lessons learned from the first exercise, says Maj. Robert Crawford, chief of Plans and Operation Branch, ISEC-EUR. "We now have a better feeling of how things would actually happen in the field," he adds. "This gives us a chance to fine tune our methods and implement them in the next exercise." |
|
|
(Source: Zweibrücken Sun, March 15, 1988) |
Kreuzberg Past and Present
By Sp4 Charles Powers and Monika Kropf
Artcile includes information on the Information Systems Engineering Command, Europe. To read article click here. |
 |
|
|
Standard Systems |
|
CAMPS - Centralized Automated Military Pay System |
|
The Centralized Automated Military Pay System (CAMPS) was also first introduced at 3rd Inf Div as a prototype site for USAREUR. With this system a 3rd Inf Div soldier's pay account is maintained on magnetic tape at the finance center in Indianapolis, Ind. There pay changes can be easily and readily updated with few errors. The system allows the soldier the opportunity to elect to be paid twice a month and even determine how much of their pay they get on payday.
Processed on the division's UNIVAC 1005, the system also processes the pay vouchers the troops get. It can run off 1,500 pay vouchers per hour. |
|
|
COSCOM - Corps Support Command Management System |
|
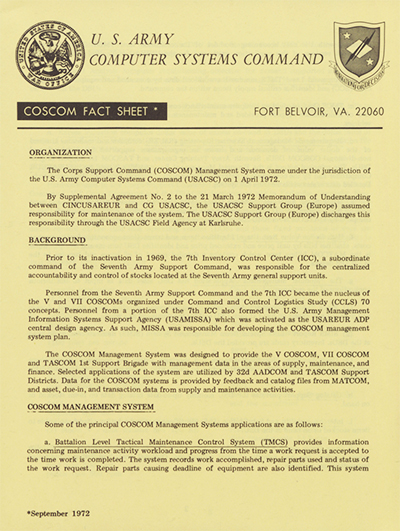
Fact Sheet: COSCOM Management System, 1972 |
|
|
|
|
1977 |
(Source: Automatic Data Processing Management Handbook, Student Text ST 18-153, January 1985) |
ORGANIZATION
In April 1972 the US Army Computer Systems Command (USACSC) assumed responsibility for maintaining the Corps Support Command (COSCOM) Management System. USACSC Support Group, Europe, located in Zweibruecken, Germany is responsible for maintaining this system.
BACKGROUND
Prior to its inactivation in 1969, the 7th Inventory Control Center (ICC), a subordinate command of the Seventh Army Support Command, was responsible for the centralized accountability and control of stocks located at the Seventh Army general support units.
Personnel from the Seventh Army Support Command and the 7th ICC became the nucleus of the V COSCOM and VII COSCOM organized under Command and Control Logistics Study 70 concepts. Personnel from a portion of the 7th ICC also formed the US Army
Management Information Systems Support Agency (USAMISSA) which was activated as the USAREUR ADP central design agency. As such, MISSA was responsible for developing the COSCOM Management system plan.
The COSCOM Management System was designed to provide the V COSCOM, 2nd Support Command (previously VII COSCOM), and 1st Support Brigade, with management data in the areas of supply, maintenance, and finance. Selected applications of the system are utilized by 32nd
AADCOM and USAREUR Support Activities. Data for the COSCOM systems is provided by feedback and catalog files from USAREUR-MMC, and asset, due-in, and transaction data from supply and maintenance activities.
COSCOM MANAGEMENT SYSTEM
The COSCOM Management System is divided into three subsystems providing Financial Management, Maintenance Management, and Supply Management Information. These sub-systems and their principal modules are as follows:
a. Financial Management:
(1) Automated Budget - provides a data bank concept capable of collecting, storing, and reporting financial data to meet the requirements of staff elements at Major HQ Budget Agencies, their subordinate commands, and HQ USAREUR.
(2) Requirements Management/Expense Reporting (RM/ER) - compiles and maintains a record of the dollar value of demands and issues to organizations supported by the Corps and the 21st Support Command DSU. The principal outputs are financial transactions for direct interface with STANFINS and the Financial Management Report which is used by USAREUR
Comptroller and by the commands to determine the amount of support furnished other commands.
b. Maintenance Management:
(1) Command Level Tactical Maintenance Control System (TMCS) - summarizes workload data by command and equipment category code (ECC) and identifies critical supply items within the command.
(2) TMCS Cost Accounting - compiles maintenance costs for the individual command, computes cost of maintenance support
provided and maintenance costs applicable to administrative motor vehicles.
c. Supply Management
(1) Asset Balance Application - edits asset records and provides DSU asset data as input to the following applications of the system:
(a) Stock Status - computes dollar value of requisitioning objective, assets on-hand, due-ins and due-outs and excess on-hand at each DSU and for the command as a whole.
(b) Cross Leveling - identifies overages and shortages within the command. Excess items meeting specified criteria are ordered
shipped to units with shortages to cross level available stockage.
(2) Catalog Support - provides the DSU monthly up-to-date catalog data on items stocked or on-hand.
(3) Due-In Reconciliation -
reconciles the DSU due-in file with the USAREUR MMC document control file and provides optional cards and listings.
(4) Excess Valuation - computes dollar value of excess on-hand at DSU and the dollar value of credit if turned in to a USAREUR MMC depot. Amount of creditable excess is based on stock position file provided by USAREUR MMC. Excess, meeting prescribed criteria, is ordered evacuated.
(5) Field Return Credit - summarizes, by command, percentages of returns to requisitions for individual NSN, giving dollar ammounts broken out by NSL and ASL items.
(6) Fund Commitment Verification (FCV) - The FCV module produces daily, weekly and monthly reports that identify the consumer funds committed for repair parts and supplies. Through the use of this system, supply and financial managers at control headquarters can determine their commands' daily financial position for applicable classes of supply. Managers can also evaluate supply performance and initiate supply economy measures.
(7) High Dollar Value Item Usage - identifies items and transactions accounting for the greatest costs, stratifies bills by unit price and extended price, and identifies DSU turn-ins and receipts. Input is the USAREUR MMC billing tape which contains a
detailed record of all issues and turn-ins to the USAREUR MMC depots.
(8) Interchangeabihty and Substitution (I&S) - identifies prime and substitute items applicable to iterns stocked or on-hand at the DSU.
(9) Supply Performance Report (SUPER) - takes unit and USAREUR MMC supply transactions, edits them and produces statistical charts of the input.
EQUIPMENT CONFIGURATION
|
|
EQUIPMENT |
V COSCOM
VII COSCOM |
21st SUPPORT
COMMAND
|
DIVISIONS |
|
CPU |
IBM 360/40
128K |
IBM 360/30
128K
|
IBM 360/30
256K |
|
TAPE DRIVES |
6 ea 2401 |
6 ea MAI (sic)
|
6 ea 2401 |
|
DIRECT ACCESS STORAGE DEVICES |
1 ea 2314 |
1 ea 2314 |
1 ea 2314 |
|
PRINTER |
1 ea 1403 |
1 ea 1403 |
1 ea 1403 |
|
CARD READER/PUNCH |
1 ea 2540 |
1 ea 2540 |
1 ea 2540 |
|
CONSOLE |
1 ea 1052 |
1 ea 1052 |
1 ea 1052 |
|
|
|
DAS3 - Decentralized Automated Service Support System |
|
1981 |
(Source: THE LOG, January 1981) |
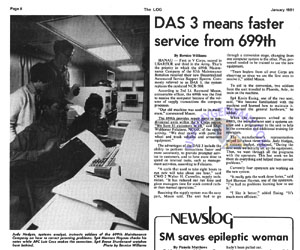 |
|
Article on the implementation of the Decentralized Automated Service Support System (DAS3) at the 699th Maintenance Company of the 85th Maint Bn.
This is the first install of DAS3 in V Corps and only the second one in USAREUR.
This system replaces the NCR 500 computer. |
|
|
ADDITIONAL ARTICLES ON DAS-3
Click here for additional information on DAS3.
Click here for information on the DAS3 at 22nd Maint Co, 71st Maint Bn |
|
|
DLOGS - Division Logistics System |
|
1969 |
(Source: ARMY LOGISTICIAN, September-October 1969) |
FACELIFTING FOR DIVISION SUPPLY SYSTEMS
Division supply systems will undergo facelifting under the Division Logistics System (DLOGS) recently approved by the U. S. Army Chief of Staff. The system, based on results of tests run at Fort Hood, Texas, automates combat service support functions on the UNIVAC 1005 computer. Scheduled for implementation in Europe, Korea, and CONUS, the system provides for —
 A commodity-oriented division supply office and a division data center equipped with UNIVAC 1005's to process personnel and pay applications and selected logistics functions.
 A property book section within the division supply office which contains the division property book officer and personnel to control and manage property book records for the division. The division property book officer — and he is the only one in the division — issues property to divisional units
on computer-produced hand receipts and provides units with a monthly update for verification and signature. The system also makes the property book officer the manager of the Army Equipment Status Reporting System (AESRS) in the division and provides for battalion roll ups to assist in unit readiness reporting.
 A central issue facility for organizational clothing and equipment operated by division supply and service company with property and reportable items records maintained by the division supply officer and the UNIVAC 1005 at division level.
 Automation of repair parts support, to include prescribed load lists. That system, known as SEACAPS, is being installed in the 24th Infantry Division
at Fort Riley, Kansas. |
|
|
1971 |
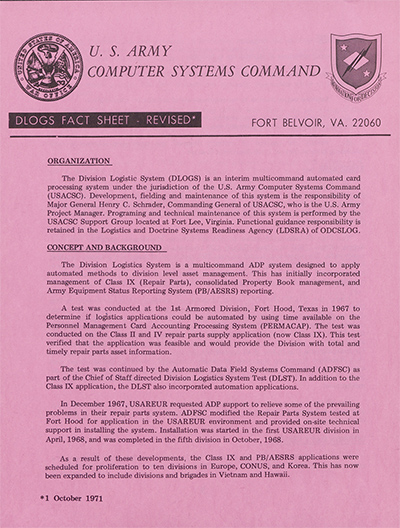
Fact Sheet: COSCOM Management System, 1972 |
|
|
1975 |
(Source: ARMY LOGISTICIAN, May-June 1975) |
|
3rd Infantry Division was the first combat division in Europe to convert to the automated property book portion of the Division Logistics System (DLOGS).
The division was alerted in April 1973 to establish a DLOGS property book activity with personnel and material to assist units in preparing for the conversion from manual to automated property records. An ad hoc committee with representatives from the Division G3, G4, Division Support Command, and the 3rd S&T Battalion was formed to accomplish initial planning.
Training on the system was accomplished during June through familiarization trips to CONUS divisions that had DLOGS property books established. Classes were also held in-country and a Computer Systems Command briefing team came to Europe to conduct personnel briefings.
|
|
"Scrubout" teams were formed and visited all unit supply activities. These teams consisted of a warrant officer, one senior NCO and a supply specialist. The teams were responsible for checking the property records of each unit to insure that all property on the property books was accounted for and the data on each property book page were accurate.
Property record conversion began in July 1973. Record conversion teams were formed and units declared "ready" by the "scrubout" teams were scheduled to deliver their property books and associated records to the division automated consolidated property book office for conversion.
Property records from the 33 battalions were broken down into 115 separate company-level hand receipts during the conversion in order to establish each company commander as a hand receipt holder, accountable to the division property book officer.
Once all data was in format for input into the automated system, it was delivered to the Division Data Center for key punching and processing, The output was a machine listing of the unit property data by company. The machine listing was then verified against the manual property books that remained in the division property book office until the final listing was produced. Once the final listings were produced they were returned to the battalion property section. After the section verified that everything was in order, the company commander signed the original copy of the listing and it was returned to the division property book officer.
Property book accountability was assumed by the division property book officer for all property except classes I, III and V and training aids.
During the conversion process, additional functional sections were formed and added to the DPBO:
Document control and editing branch - this section received and logged all data received from or transmitted to the conversion teams; it also received, edited, and forwarded unit requests for supplies to the appropriate supply support activity for action. (Close coordination with SSAs was maintained to insure continuing supply support during the conversion period.) All machine listings, adjustment documents, and supply requests are routed through the document control and editing branch.
Property book asset management teams - as soon as a unit's property records had been converted, a property book asset management team was formed from personnel of the "scrubout" team that had completed its requirements. The team established close liaison with unit supply activity that had been converted to insure minimum interruption in logistics support to the unit. It is the property book asset management team that carries on the day-to-day property book supply action for the units that they are designated to support. Each team consists of a warrant officer team chief, a senior supply sergeant, a senior supply specialist, and a supply specialist.
As a result of the implementation of DLOGS in the 3rd Infantry Division, there is
 one primary source of supply and equipment data availbale to commanders at each level;
 one activity through which each unit supply section must process supply requests for property book items;
 a consolidation of supply personnel that has reduced the number required within the division,
|
|
|
1980 |
(Source: Automatic Data Processing Management Handbook, Student Text ST 18-153, January 1985) |
ORGANIZATION
The Division Logistics System (DLOGS) is an interim multicommand automated card processing system under the jurisdiction of the US Army Computer Systems Command (USACSC). Development, fielding and maintenance of this system is the responsibility of the Commanding General of USACSC, who is the US Army Project Manager. Programing and technical maintenance of this system is performed by the USACSC Support Group located at Fort Lee, Virginia. Functional guidance
responsibility is retained with the US Army Logistics Center (LOGC) at Fort Lee, under the functional
proponency of DA DCSLOG.
CONCEPT AND BACKGROUND
The Division Logistics System is a multicommand ADP system designed to apply automated methods to division level asset management. This has initially incorporated management of Class IX (Repair Parts), consolidated Property Book management, and Army Equipment Status Reporting System
(PB/AESRS) reporting.
A test was conducted at the 1st Armored Division, Fort Hood, Texas, in 1967 to determine if logistics applications could be automated by using time available on the Personnel Management Card Accounting Processing System (PERMACAP). The test was conducted on the Class II and IV repair
parts supply application (now Class IX). This test verified that the application was feasible and would
provide the division with total and timely repair parts asset information.
The test was continued by the Automatic Data Field Systems Command (ADFSC) as part of the Chief
of Staff directed Division Logistics System Test (DLST). In addition to the Class IX application, the
DLST also incorporated automation applications.
In December 1967, USAREUR requested ADP support to relieve some of the prevailing problems in
their repair parts system. ADFSC modified the Repair Parts System tested at Fort Hood for
application in the USAREUR environment and provided on-site technical support in installing the
system. Installation was started in the first USAREUR division in April, 1968, and was completed in
the fifth division in October, 1968.
As a result of these developments, the Class IX and PB/AESRS applications were scheduled for
extension to eleven divisions in Europe, CONUS, Pacific and the Combat Equipment Group,
Europe.
In Calendar Year 1974, the DLOGS 1005 system was translated from the UNIVAC 1005 programing
language to IBM 360 assembly language. The IBM 360 version of DLOGS now serves as the supply
system of record in the CS3 system which is presently being extended to the active Army divisions.
The DLOGS system in the CS3 environment is the same as the DLOGS on the UNIVAC 1005 and thus
is transparent to the user.
OBJECTIVES
The overall objectives of DLOGS are as follows:
a. Standardize logistics systems, methods, and procedures at division level worldwide.
b. Improve responsiveness to the requirements of installation commanders.
c. Provide installation commanders with standard automated systems that will support their missions in an effective and economic manner.
d. Fortify the concept of centrally designed and maintained automated data processing systems that are multi-functional in scope.
FUNCTIONS
The initial DLOGS systems provide automated processes which supplant the manual procedures previously employed at division level for management of Repair Parts, maintenance of Property Books,
and preparation of AESRS reports. Other applications, including Country Store and Class I, III, and
IV management systems are projected for future consideration.
The Class IX automated system permits the Division's Repair Parts Managers to utilize DLOGS ADP
processes for more efficient management of repair parts. The automated system relieves management
personnel of many of the routine detailed tasks inherent in the manual procedures. This reduces the
probability of human error and provides more accurate and timely asset management data. Daily
machine runs provide complete asset status listings of Repair Parts for Repair Parts personnel and
other division elements.
Under the DLOGS Property Book concept, all management is transferred to the Division Property
Book Officer (PBO), who maintains Property Book Accountability for the division. Property Book
accountability is maintained under the provisions of AR 735-35 and necessary information is maintained on ADP listings. Consolidated listings are maintained in the office of the PBO. Hand receipt
listings for each company commander provide complete and current property data at that level. The
Property Book Management System provides for maintaining a Due-In file of all expendable requisitions, and provides elements for the Unit Readiness Reporting that were previously calculated
manually. Centralization and automation of Property Book accountability are designed to provide
positive control of assets for the Division Supply Office (DSO) and furnish maximum efficiency in
records management.
The DLOGS system introduces an automated method for extracting asset data from ADP records for
the Army Equipment Status Reporting System reports. Previously this was obtained manually.
DIVISION DATA CENTER
Under the DLOGS concept, the data base for functional management is developed in a central Division Data Center (DDC). The DDC is assigned the exclusive responsibility of processing systems input data prepared by functional managers and developing outputs for use by these managers.
The DDC is managed by an ADP qualified officer who directs the processing of the DLOGS and other
automated processes for optimum efficiency and utilization of available machine time. All operating
schedules are controlled by the Chief of the DDC.
EQUIPMENT CONFIGURATION
The ADPE for DLOGS (1005) consists of a UNIVAC 1005 card processor, auxiliary card reader, card
punch, and IBM peripheral equipment consisting of 557 Interpreter, a 188 Collator, 083 and 084
Sorters, key punches and verifiers. The DLOGS (360) system runs on the IBM 360 series. In active
Army divisions it operates within the CS3 van mounted configuration. All vans in both configurations
are equipped with air conditioners and heaters. Portable generators provide operational capability in
areas where commercial power is not available or its use is not practical. For tactical security units
may disperse in any location near the division area of operation and continue to function effectively.
DLOGS USERS
The DLOGS 360 system is operational in divisions in Korea, Germany, CONUS and Hawaii. The Class
IX system was extended to USARV in June 1972 until the cessation of hostilities and then phased out
of Vietnam. The DLOGS 1005 system is being extended to National Guard and Reserve Divisions.
The Division Support Command uses the DLOGS Class IX application for repair parts management.
Input data is forwarded daily to the DDC for processing. The various types of input required for repair
parts management are developed in a daily cycle and disseminated to various users in the Army Supply
System. Transaction listings and other supply management data are developed daily to provide repair
parts managers information possible for repair parts management.
The Division Property Book Officer uses the DLOG System to maintain a centralized property book in
the division. The automated system maintains a master Property Book Record for the Division Property Book Officer, Company Property hand receipt listings for each company commander, and
battalion roll-up. The AESRS Report is developed from the master Property Book Records. |
|
|
DS4 - Direct Support Unit Standard Supply System |
|
(Source: Zweibrücken Sun, April 30, 1984) |
User symposium conducted
Haven't you ever wanted to talk with the inventor of something that you use frequently? A number of supply personnel throughout Europe had the opportunity last month to discuss their DS4 systems with the people who write the programs for the DS4.
The DS4, or Direct Support Unit Standard Supply System, is essentially a computer that is programmed to process and store detailed information of supply items for the Active Army, Army Reserve and National Guard Units.
Computer Systems Command here hosted the symposium, which was held in Homburg. According to CW2 Joe Galloni, Chief of the Honeywell Systems Team, DS4 "users", as they are termed, are actually supply personnel who have been placed in numerous vans throughout Germany to operate the Honeywell computer.
"Consequently, when you have individuals who haven't been trained for the equipment they are operating, problems will arise. The symposium allowed all the users to finally gather together, giving them an opportunity to discuss any technical or functional problems they've experienced," Galloni explained.
Personnel from the Assigned Software Developer and the Logistics Center from Fort Lee, Va. attended the symposium to answer questions or solve problems the users might have experienced with their systems. These people make long-term corrections through-out the system; the Computer Systems Command personnel on Kreuzberg assist users with short-term corrections.
Galloni said that the users would like to have another symposium in the future, when the next book of corrections from Fort Lee is dispensed throughout the system. |
|
|
PERMACAP - Personnel Management and Accounting Card Processor System |
|
The Personnel Management and Accounting Card Processor (PERMACAP) system was first introduced at 3rd Infantry Division in Würzburg (in 1967). 3rd Inf Div was selected by USAREUR as the prototype site to provide a valid test of PERMACAP.
This system runs on a UNIVAC 1005 Card Processor (Webmaster note: installed at the division's Adjutant General section?) and eliminates the manual entry of numerous data on unit morning reports, thus increasing the accuracy and speed of the process. It also produces recurring reports and rosters for personnel management used within the division and sent up to HQ USAREUR.
The Morning Report is a daily strength accounting system. |
|
|
(Source: Provision of Personnel and Administrative Support to the Forward Deployed Force, by Maj William V. Green, June 1975) |
In 1974/75, most USAREUR units were (still) using the PERMACAP System supported by the UNIVAC 1005 Card Processor. |
|
|
TRANSCOM - Theater Army Support Command (Transportation) |
|
1976 |
(Source: Automatic Data Processing Management Handbook, Student Text ST 18-153, January 1985) |
ORGANIZATION
In April 1972, the US Army Computer Systems Command (USACSC) assumed responsibility for the maintenance of the Theater Army Support Command (Transportation) (TRANSCOM) Computer System. The USACSC Support Group Europe is responsible for the continued maintenance of the TRANSCOM system.
The TRANSCOM system provides ADP support to the Transportation Division, DCSLOG Hqs USAREUR, Heidelberg, Germany; 4th Transportation Brigade, Oberursel, Germany and the 37th Transportation Group, Kaiserslautern, Germany.
BACKGROUND
USAREUR transportation activities plan, manage and operate an integrated transportation service to meet the theater requirements for movement of personnel and material consistent with economy and established priorities.
Prior to the deactivation of the US Army Traffic Management Agency in January 1969, the traffic management and movement control missions were historically dependent on external agencies for ADP support. This dependency included system design, programing and processing performed in many geographic locations on diverse data processing equipment. In January 1969 USATRANSCOM was activated and staffed to provide data systems support for transportation management. At the time of activation the bulk of data processing support was provided by the Hessen Support District Service Center in Frankfurt and the MATCOM Data Processing Center at Zweibruecken with several outlying agencies providing miscellaneous support.
In January 1971 , the data processing support for USATRANSCOM was transferred to US Army Management Information System Support Agency (USA-MISSA). On 1 April 1972, the US Army Computer Systems Command assumed responsibility for the maintenance of TRANSCOM. Support of the system included responsibility for the port systems at Rotterdam and Bremerhaven.
The port systems were replaced by the DA Standard Port System (DASPS) as part of the development of the US Army standard Terminal Operations and Movements Management System (TOMMS).
The DASPS system is maintained and supported by USACSC Support Group, Ft Lee, Virginia with USACSC Support Group Europe performing only a Customer Assistance role through its on site representative at Bremerhaven.
THE FUNCTIONAL SYSTEM
The TRANSCOM system can be categorized into the major subsystems shown below:
a. Sea Van Management Information.
b. Cargo Traffic Analysis
c. Transportation Performance Analysis
d. Passenger Traffic Analysis
e. Table Maintenance and Retrieval
f. Highway Fleet Management
g. Passenger Reservation
h. Household Goods and Baggage
i. European Activity Address
j. Administrative Use Vehicles
For operational purposes, these subsystems are further subdivided into production cycles. Some of the principal cycles and run frequencies are:
a. Sea Van Management Information (SEAMIST). This subsystem consists of daily, weekly, monthly and as required processing cycles which monitor commercial SEAVAN container traffic for all DOD sponsored cargo moving into and out of the theater. Current status of each container is maintained from vessel discharge, port departure, arrival at final destination, unstuffing and release to the carrier or return under load to CONUS. Products produced are used to ensure timely arrival and preclude congestion at destination, to monitor the unstuffing and timely release to carrier and as a source of traffic information.
b. Cargo Traffic Analysis (CTA). This subsystem consists of monthly, quarterly and yearly processing cycles which compile traffic data on cargo moved via military highway and commercial modes in the European area. Products produced are used to monitor mode and route selection, positioning of military transportation assets and in negotiating favorable commercial rates and conditions.
c. Transportation Performance Analysis (TPA). This subsystem is used to accumulate intransit times required for within theater movement of cargo and to measure these times against established intransit standards. Products produced are used in evaluating the total order and shipping time performance and improving the timeliness of transportation service.
d. Passenger Traffic Analysis (PTA). This subsystem is a monthly processed management information system which compiles data on intra-theater passenger traffic via commercial carriers. Products are used as a basis for negotiating advantageous terms and to ensure favorable application of existing terms and mode options. (Currently this subsystem is not in use.)
e. Table Maintenance and Retrievel (TMARS). This subsystem is a data management application which maintains parameters, stored tables and data files on disk data sets in a fashion which allows other TRANSCOM subsystems access to a common central repository of consistent table and driver information required for TRANSCOM processing. In addition to updating and maintaining the disk data base, this subsystem will, through use of "call" options in problem
programs of the other subsystems, perform table look-up and retrieval functions and return table records or a combination of records to the requesting program.
f. Highway Fleet Management (HFM). This subsystem consists of daily, weekly and as required cycles which provide up-to-date information on all trailers and status of commitments to
haul cargo. Daily installation situation reports, yard check, driver reports and other input documents are processed to update both trailer location and commitment records. Performance evaluation reports and input for the TPA and CTA subsystems are produced in this application.
g. Passenger Reservation Subsystem (PAX). This subsystem consists of daily, weekly, monthly and as required processing cycles which process requests for port calls for movement of Army sponsored personnel and their dependents departing the theater to ensure proper submission of requests and issuance of confirmation; collect information on no-shows and produce confirmation of separatees departure reports and other statistical and special managerial reports
used to monitor the operation and disseminate movement projections.
h. Household Goods and Baggage (HGB). This subsystem provides management with information and statistical data on the performance of reporting activities, major commands and the operating theater as to the amount of household goods and baggage handled. Additionally,
commercial carriers involved in government contracts for movement of HGB are evaluated for performance.
i. European Activity Address File (EURAAF). This subsystem is designed to maintain a data base record for each European activity address as well as selected non-European addresses. The Joint Traffic Management Agency (JTMA) is the European dissemination and control agency for changes to the EURAAF and submission to LSSA of changes to the DODAAF. This subsystem supports this effort and the products produced are used to monitor and control all activity address actions to include the preparation of USAREUR Regulation 55-5 and supplements thereto.
j. Administrative Use Vehicles (AUV). This subsystem is designed to maintain a record of all commercial vehicles in the USAREUR inventory, provide required data to the Maintenance Management Center, Lexington, Kentucky and to provide information regarding these vehicles to the functional proponent, HQ USAREUR, ODCSLOG, Transportation Division.
EQUIPMENT CONFIGURATION
The operating environment for TRANSCOM subsystems vary but all are constrained to operate
on the expanded IBM system 360-30 (128K) DOS machine. Subsystems are upward compatible however, and can run on larger OS/DOS machines. All subsystems except HFM and AUV are
currently operational at the ADP Service Center in Zweibruecken, Germany on 360-50 OS machines utilizing dedicated 360-20 terminals at Oberursel and Zweibruecken, Germany to accomplish I/O data transfer.
The HFM subsystem is operational at the Kaiserslautern Army Depot, Germany on a 360-40 OS machine configuration. The AUV subsystem is operational at the IDHS site in Heidelberg,
Germany on a 360-50 OS machine configuration. |
 |
|
|
Automatic Data Processing Hardware |
I |
IBM System/360 Model 40 |
|
Click here for articles on the IBM 360/40 at the V COSCOM Data Processing Company. |
|
|
UNIVAC 1005 |
|
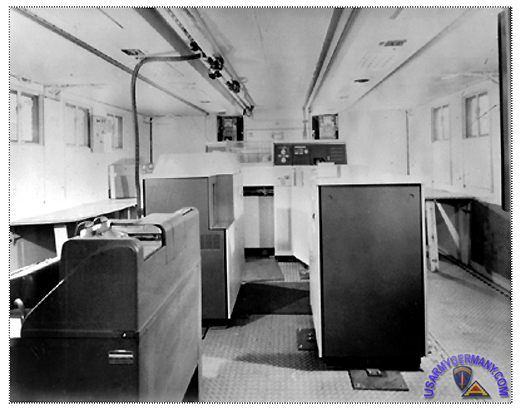
Interior view of a UNIVAC 1005 computer van
|
|
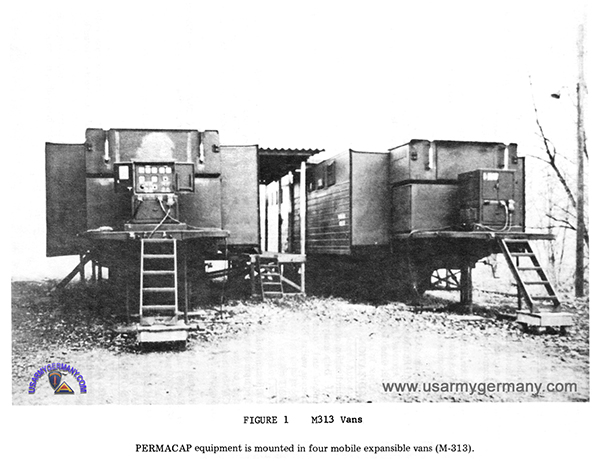
PERMACAP equipment using the UNIVAC 1005 system was installed in four M-313 vans |
|
The UNIVAC 1005 computer equipment was housed in four large standard Army expandable vans that provided it mobility. The system was equipped with a card processor, punch and reproduction unit, plus an auxiliary card reading unit. It was three times faster than the (punched card machine) equipment previously used by the divisions. It had a 4000-position memory bank; could process more than 200 cards a minute; and print 600 lines per minute.
Five groups of specially trained personnel were responsible for keeping the computer in operation:
Operators
Programmers
Key Punch Operators
Systems Analysts
Maintenance personnel
In 1966, 3rd Inf Div was the first division in USAREUR to receive a UNIVAC 1005. It served as the prototype site for PERMACAP.
In 1967, 4th Armd Div AG Section was scheduled to receive a UNIVAC 1005 card processing unit to run PERMACAP and CAMPS.
In 1968, 3rd Inf Div was the first USAREUR division to receive a UNIVAC 1005 for automation of the repair parts supply system.
(Previously, an IBM computer was used for this task ... or should that be transceiver?)
In 1968, 24th Inf Div (Fwd) was using a UNIVAC 1005 for automation of the repair parts supply system.
|
|
Related Links
Article: Computers in Vietnam (Military Review, September 1968)
|
|
|
CS3 - Combat Service Support System |
|
1972 |
(Source: STARS & STRIPES, Feb 1, 1972) |
Four IBM 360-40 computers will be assigned to the four USAREUR combat divisions (1st and 3rd Armd Divs; 3rd and 8th Inf Divs) over the next two years under a program known as Combat Service Support System. In each of the divisions, one 360/40 will replace two smaller UNIVAC 1005 units now in operation within each division. The first computer is scheduled to arrive in October.
The IBM 360/40 will provide the division with instantaneous information in the fields of supply, personnel, maintainance and financial data. Units within the division will have access to this data via tele-processing terminals (as described in the article: electronic TV-like apparatus linked directly to the computer's memory). |
|
|
1975 |
(Source: STARS & STRIPES, Nov 1, 1975) |
The Combat Service Support System (CS3) is a mobile computer system designed to process logistics, maintenance and personnel data for combat divisions. The 1st Armd Div will be the first USAREUR division to receive it. (Webmaster note: Is the article on the IBM 360/40 (above) related to this action? Could it be that the implementation was delayed for several years?)
The CS3 system replaces two UNIVAC 1005 computers (card systems) that are currently used by the 1st Armored Divison. One is installed at Ansbach and handles personnel data for the division. The other unit is located at Monteith Barracks (home of the Division Support Command and site of the Division's data center) and processes logistics data.
The new system will be located in one location and is set up in two 35-foot long vans (with an air suspension ride system). It has two generators for supplying power. The $1.2 million system is mobile and can be moved into the field with the soldiers.
The other combat divisions within USAREUR will receive the system by next May. |
|
|
NCR 500 |
|
1969 |
(Source: STARS & STRIPES, July 10, 1969) |
There are four NCR-500 computers scheduled to be installed at the 85th Maint Bn in the near future. The first one is slated to be installed and become fully operational within the next 90 days at B Company. Because of its workload, the same company will receive a second NCR-500 soon thereafter. Later this summer, A and C companies will each receive one NCR-500 system.
With the installation of the NCR-500, B Company's supply activity will be the first of 35 supply activities within V Corps to be computerized. The $53,000 NCR-500 system, with its filing and software support components, will be housed in two large tractor-drawn, air-conditioned vans.
The 85th Maint Bn is responsible for providing supplies, everything from nuts and bolts to highly sophisticated electronic and aircraft parts, to 128 non-divisional units throughout V Corps. The battalion manages a $400,000, 5000-item inventory that turns over about 10 times a year. B Company, the battalion's busiest company, processes some 12 to 15 thousand requisitions a week, with personnel working 18 to 20 hour days. With the new system, these requisitions will be processed in as little as 4 hours with an anticipated increase in accuracy of abou 30 percent.
Process: when a unit serviced by the battalion needs a part they select a card with the (stock) number of the item needed from the pre-supplied stock of punch cards, fill in the quantity needed and the date and submit it to the supply activity. The cards already supplied to each unit have the unit's code number and other necessary information on them. Each request run through the system is then recorded on a stock control ledger card. Each ledger record contains the vital information about the stock item requisitioned both on magnetic strips printed on the back and in readable print on the front. The magnetic strips are read by the machine, the readable portion is used by human operators. The ledger cards replace the five manually prepared forms used by the old system. The net result will be a release order for the item to be sent to the supply point. |
|
|
1970 |
(Source: STARS & STRIPES, May 4, 1970) |
2nd Bn, 56th Artillery, a Nike-Hercules air defense unit, is the first 32nd AADCOM unit to receive an NCR 500 computer system.
The computer was installed in January at the unit's Direct Support Platoon. |
|
|
(Source: STARS & STRIPES, June 23, 1970) |
Non-divisional direct support units-general support units (DSU-GSU) are being converted to NCR 500 computers to automate the repair parts (Class IX) supply process. (Combat divisions in USAREUR use the larger UNIVAC 1005 for this same process.) |
 |
|
|
Related Links:
|
|
|